How motherboards are designed and manufactured: inside MSI
We traveled to MSI's factory in China and offices in Taiwan to see both R&D and production for motherboards.
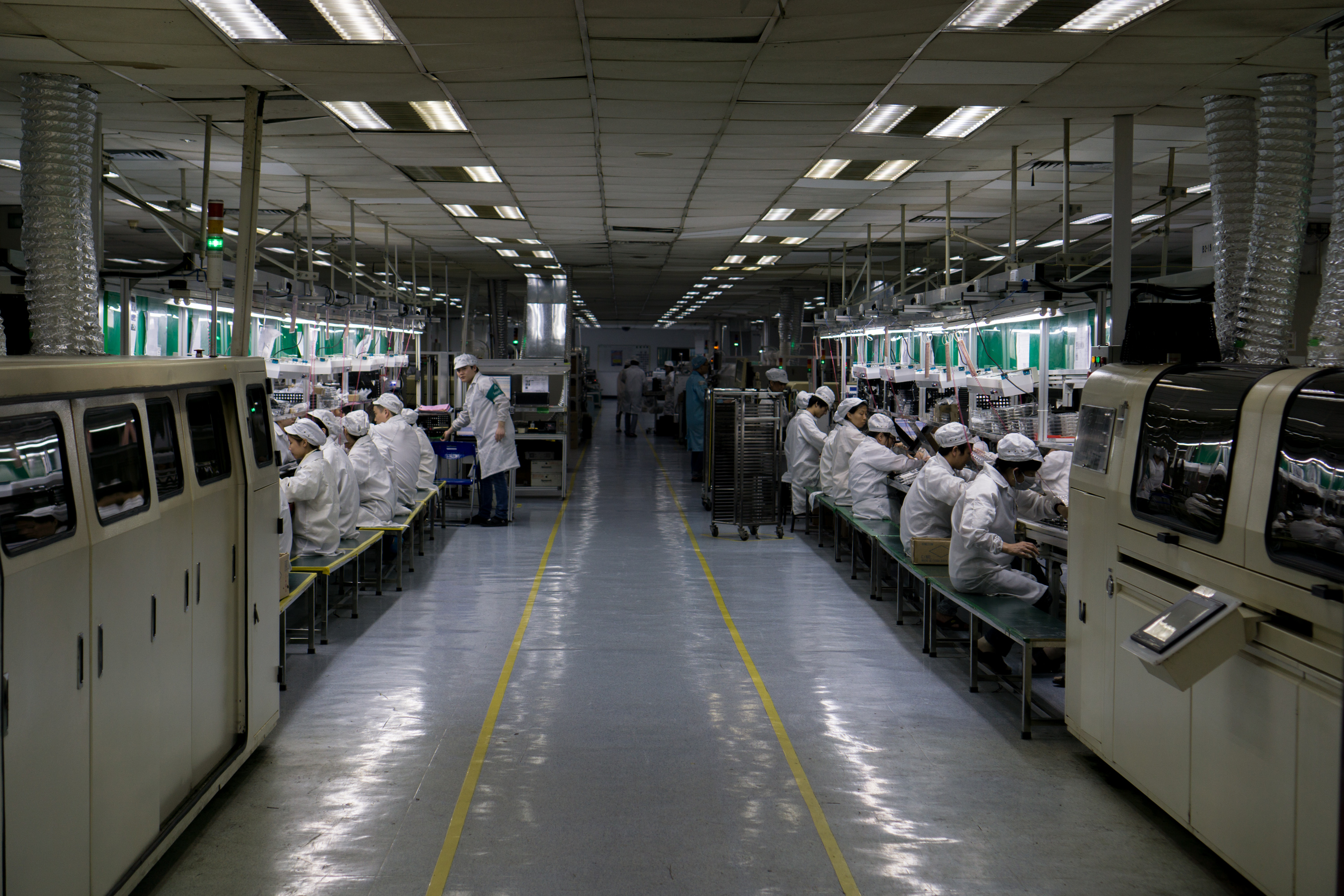
MSI’s manufacturing facility outside Shenzen, China is massive. Seriously: the complex, which I visited in late May, currently houses approximately 7000 employees, according to the facility’s director. Many of those employees work to produce thousands of motherboards and graphics cards every single day, along with full tower PCs, all-in-ones, and vehicle entertainment products (though we know them as a computer hardware company, MSI makes many other products in China, too).
I traveled to MSI’s factory to see how it builds motherboards, and how its process has changed in recent years to make MSI a stronger competitor to Gigabyte and Asus. For a fun comparison, look at MSI’s facility in the following gallery side-by-side with our tour of Gigabyte from 2015. If you’re interested in more than motherboards, stick around for the last 11 slides in the gallery, which are from MaximumPC EIC Tuan Nguyen’s trip to another MSI facility, their office in Taiwan, where he got to see their R&D and design process.
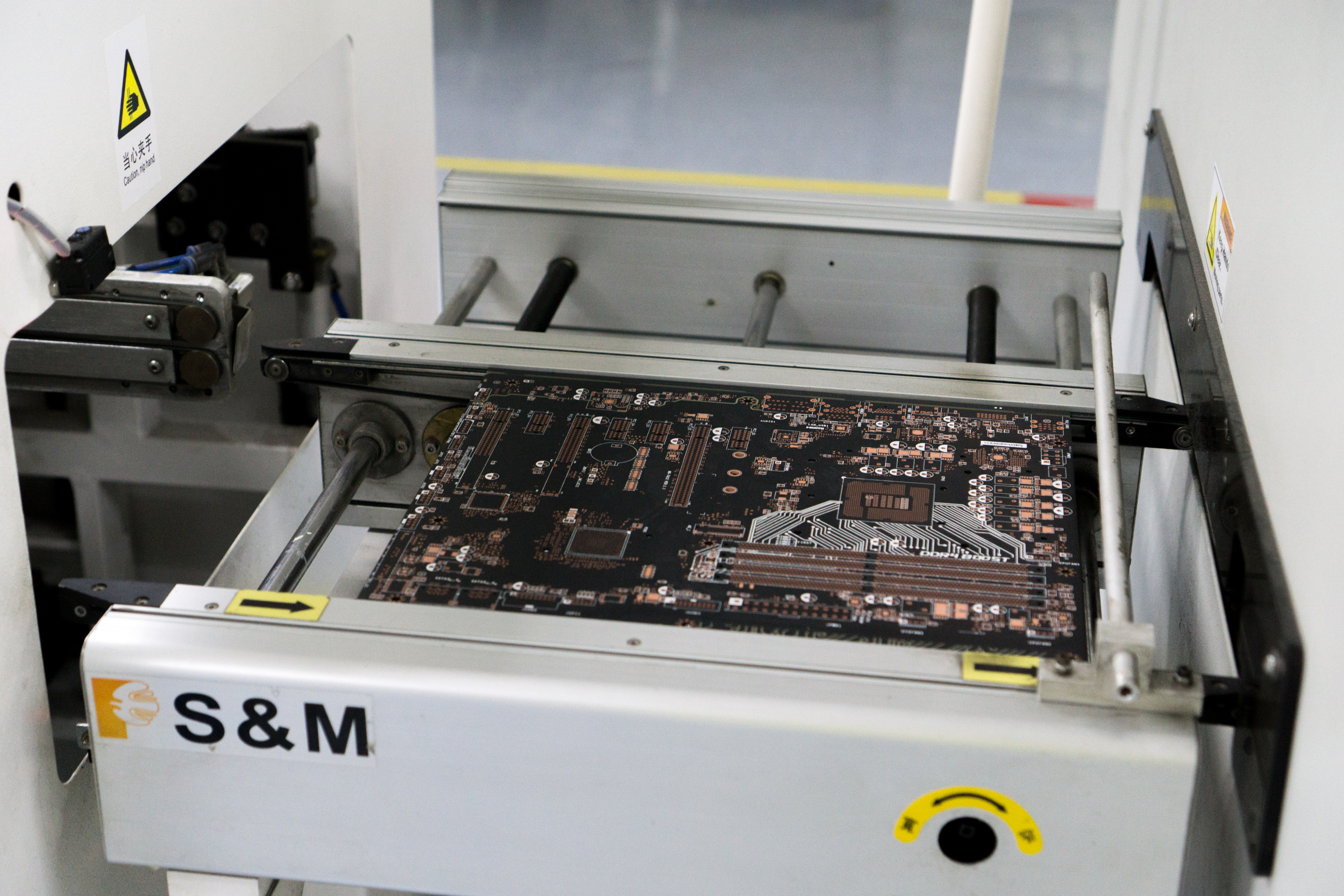
Ah, the beginning of the assembly process. Here's the beginnings of a motherboard: sourced from a PCB supplier with many of its tracings already in place, but a long way to go before it's component complete.
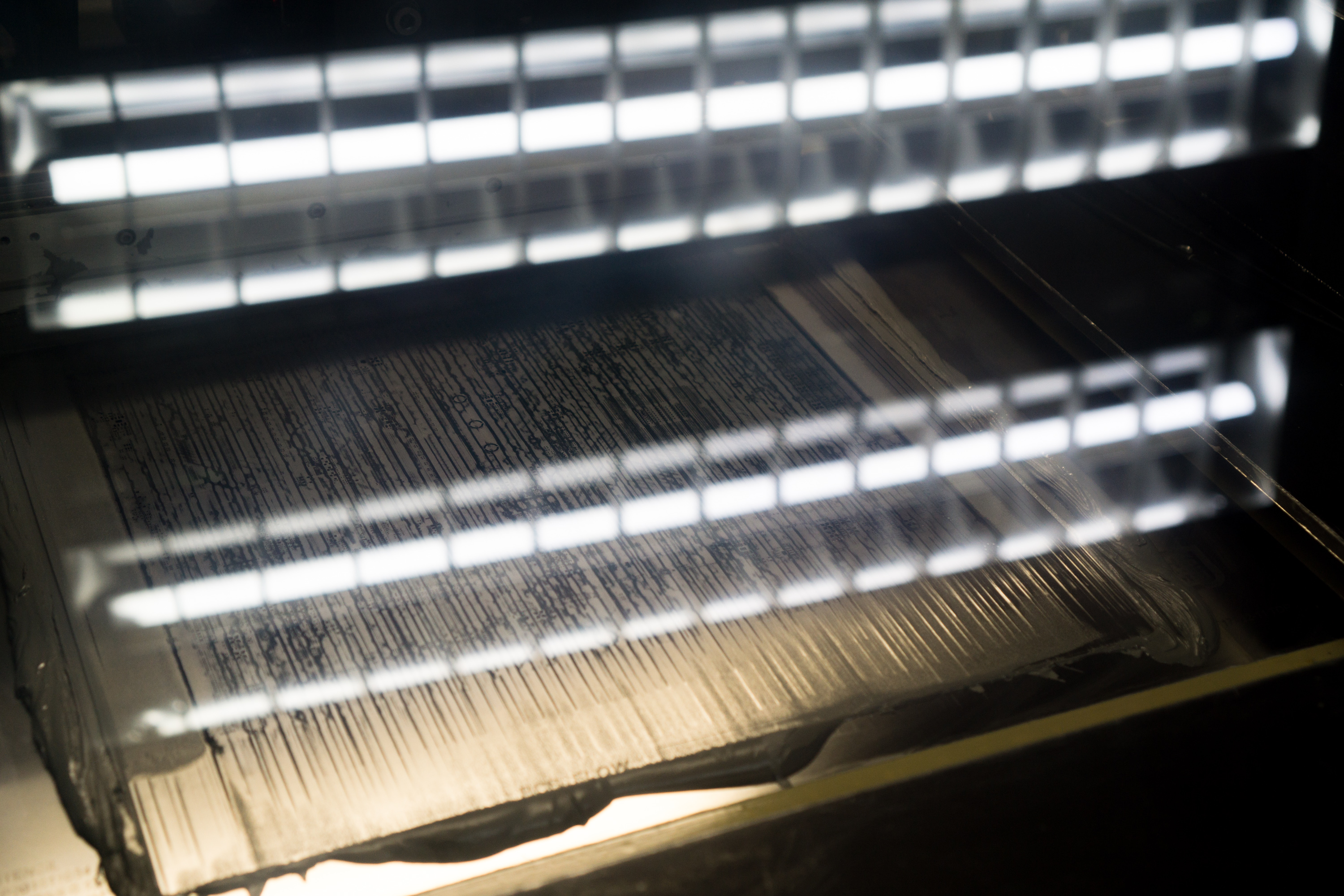
First step: the naked PCBs need to get dressed, and for motherboards that means applying solder. The first machine the boards travels through uses this tracing to apply a solder material across the surface of the board. You can see more of it in the next step.
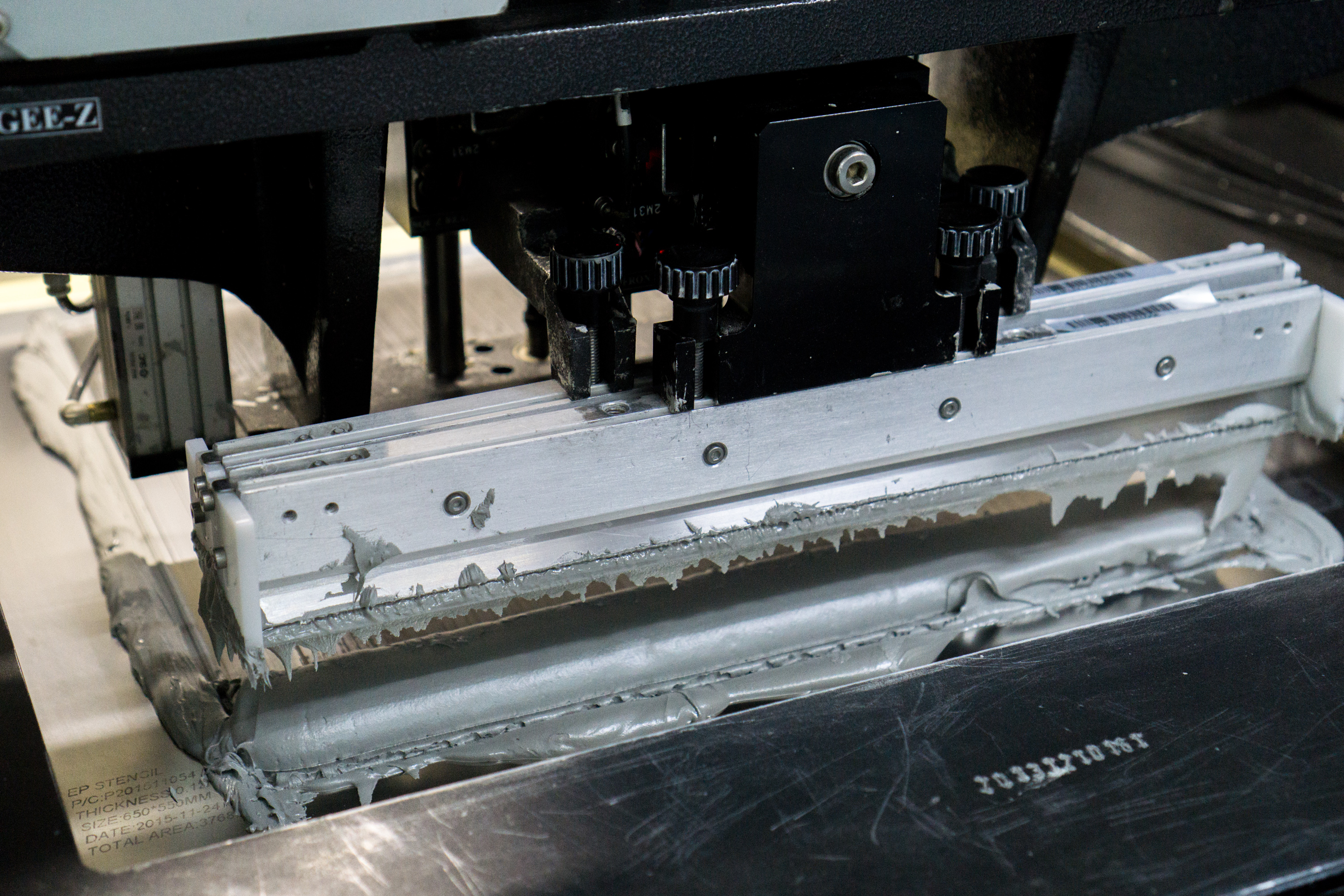
Solder paste material in the process of being applied.
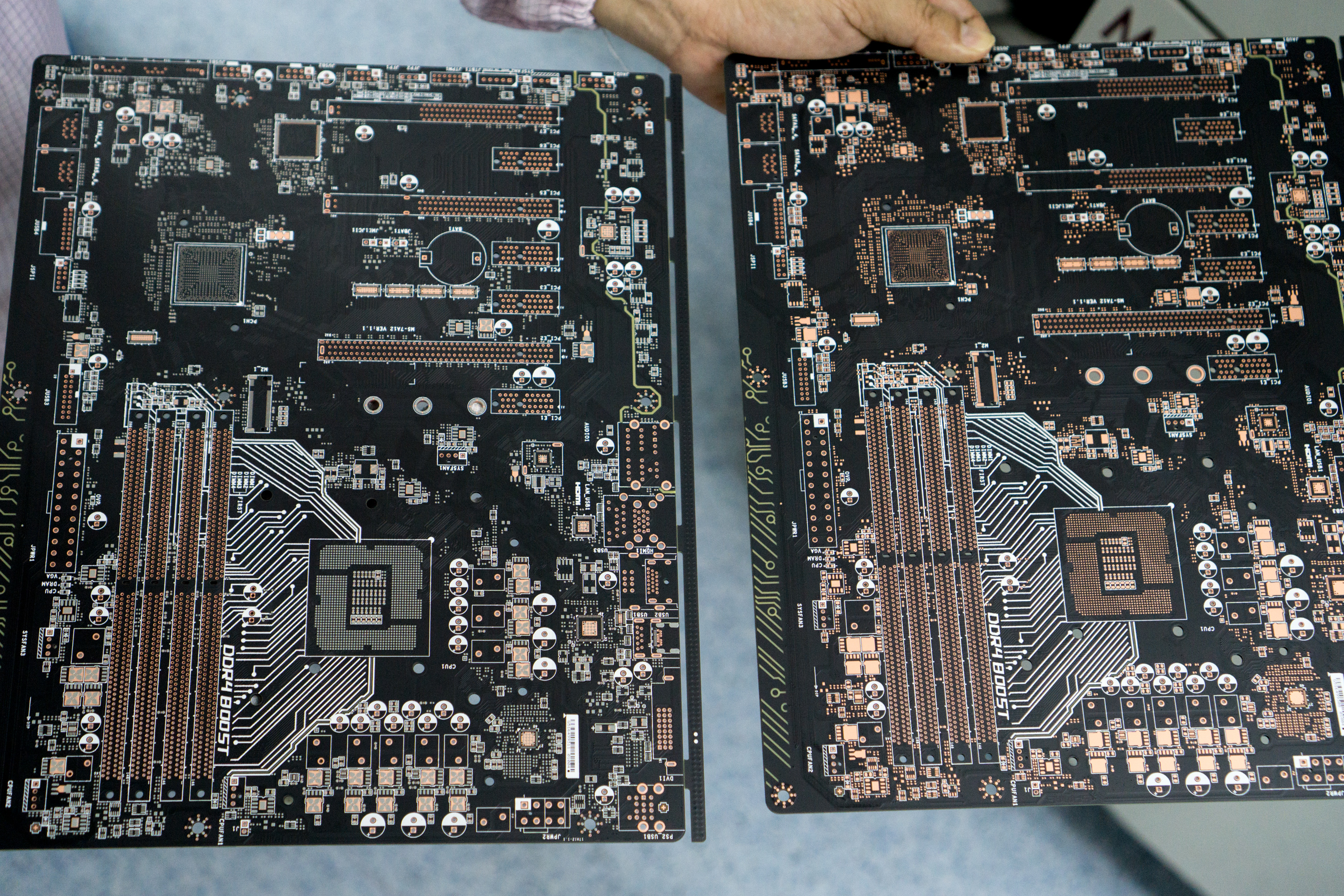
Left: a motherboard fresh off the assembly line. Notice the presence of grey solder across the board, compared to the un-soldered PCB on the right? Once it's been soldered, the board rolls down the assembly line into the next set of machines.
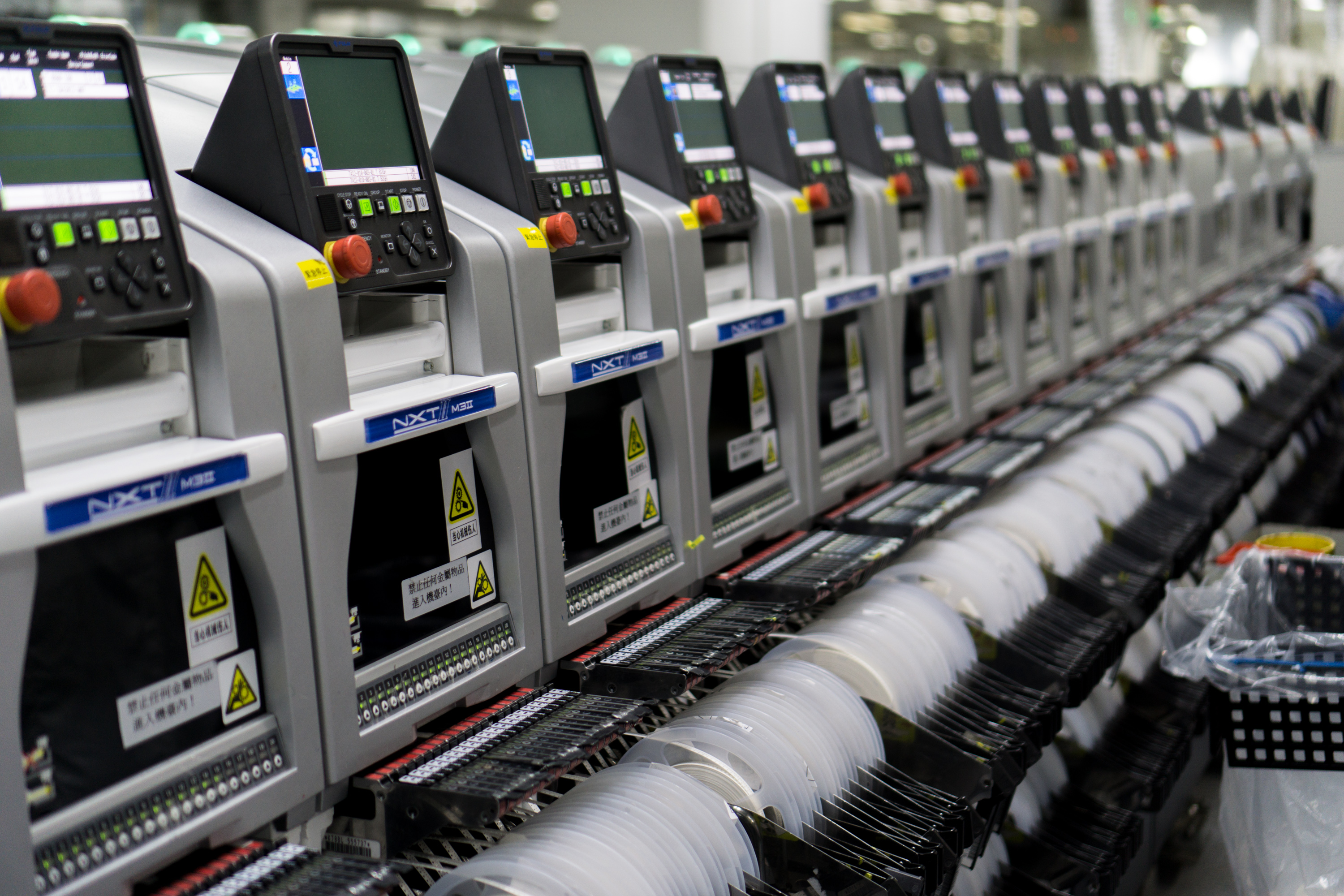
These pick-and-place machines have thousands of tiny electronic components on those reels in front. The reels are fed into the chamber and slotted into place on the motherboard. All those tiny resistors and other chips scattered across the motherboard are attached in these machines in a very fast automated process.
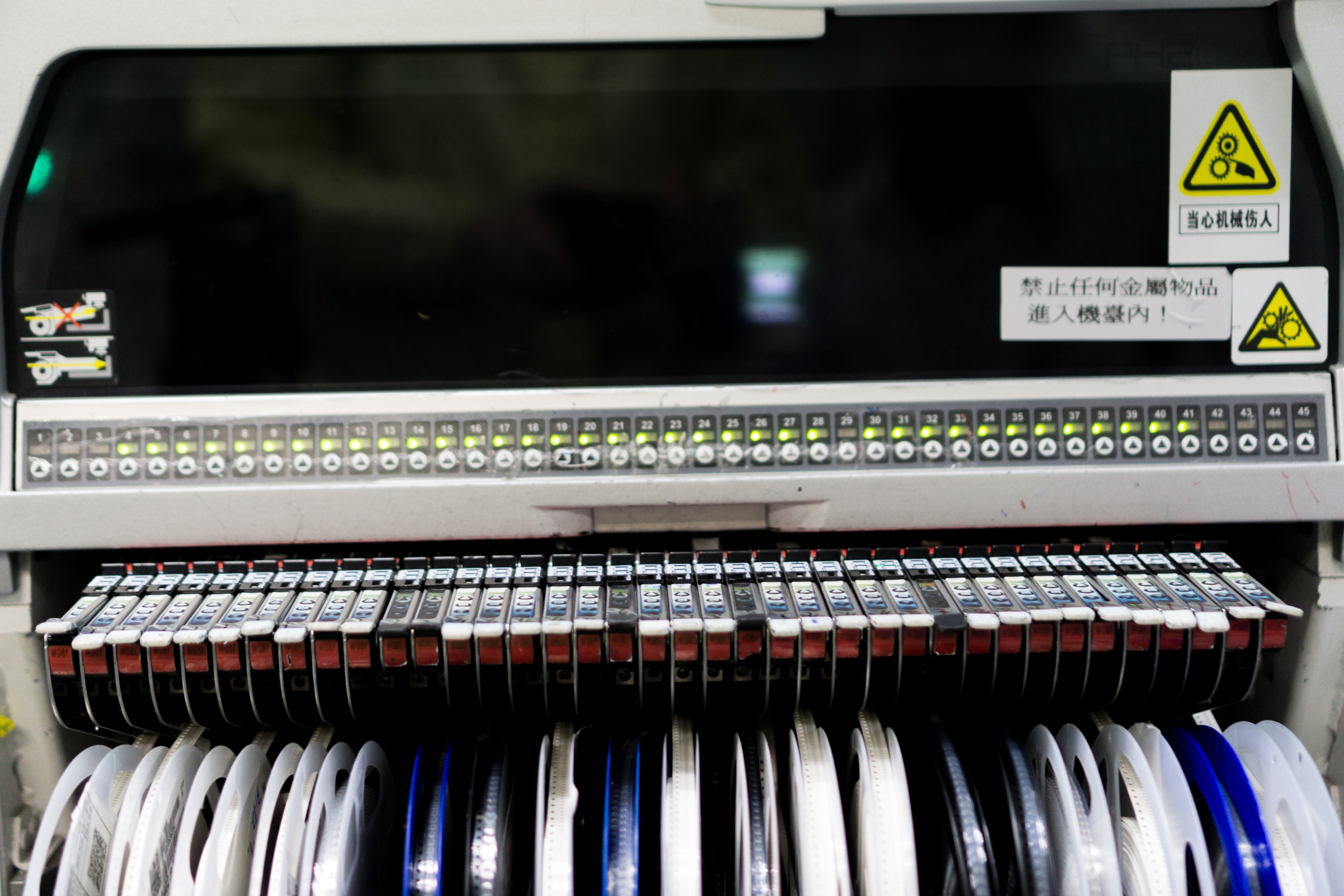
A close up of a pick-and-place machine, also referred to as a chip shooter. You can read more about the SMT (surface mount technology) process here. You can't see inside, but there's a conveyor belt rolling the through with the motherboards.
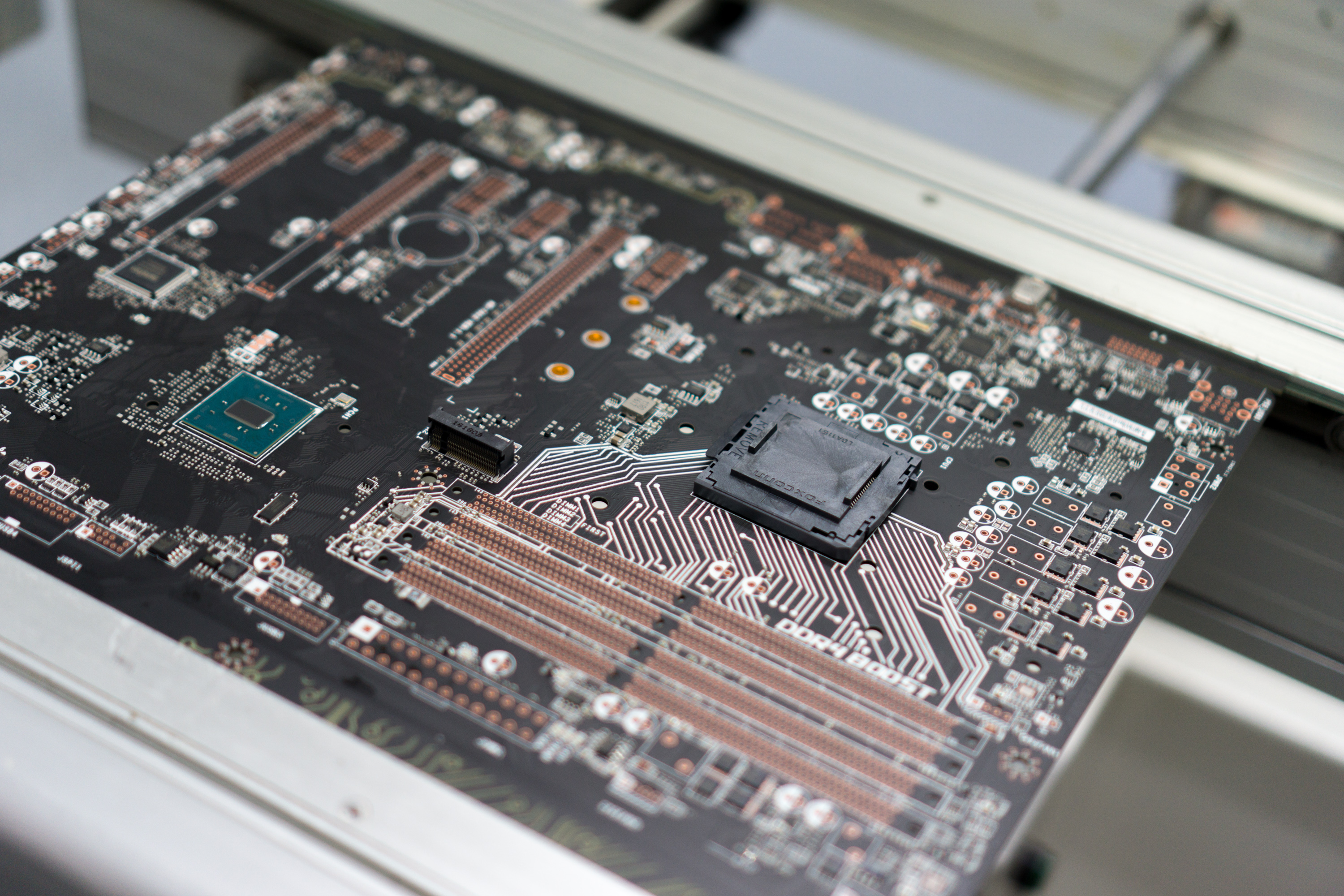
And voila: a motherboard comes out the other side covered in small bits of circuitry.
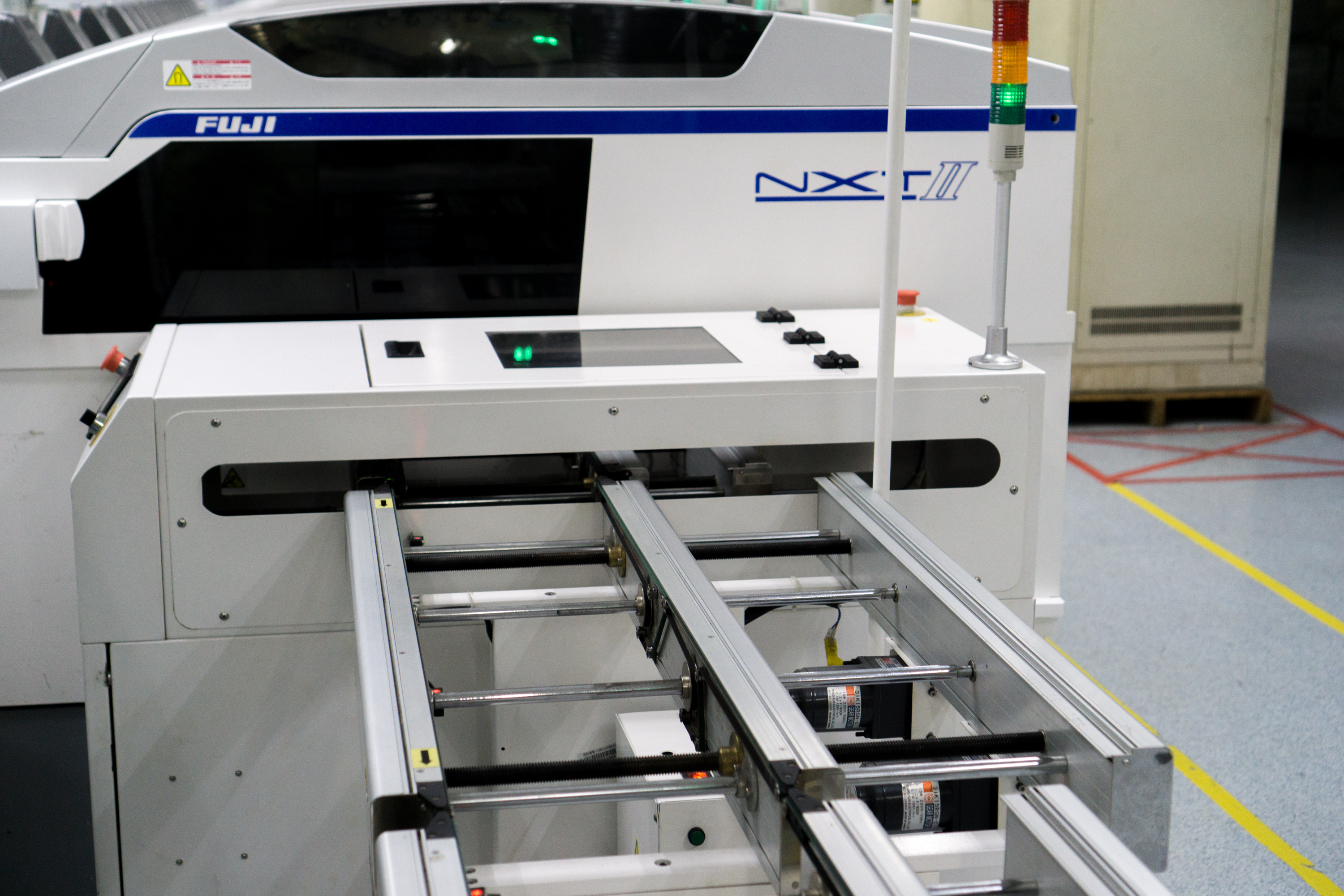
A look back at the side of the pick-and-place machine, where motherboards emerge once they've been imprinted with circuitry.
According to manufacturer Fuji's website, the NXT III (the successor to the machine pictured above) can place 37,500 chips per hour, 44 percent faster than the NXT II. There's also a great video at the link above that shows the robotic mounting arm inside placing those chips. As you can imagine, it's pretty fast.
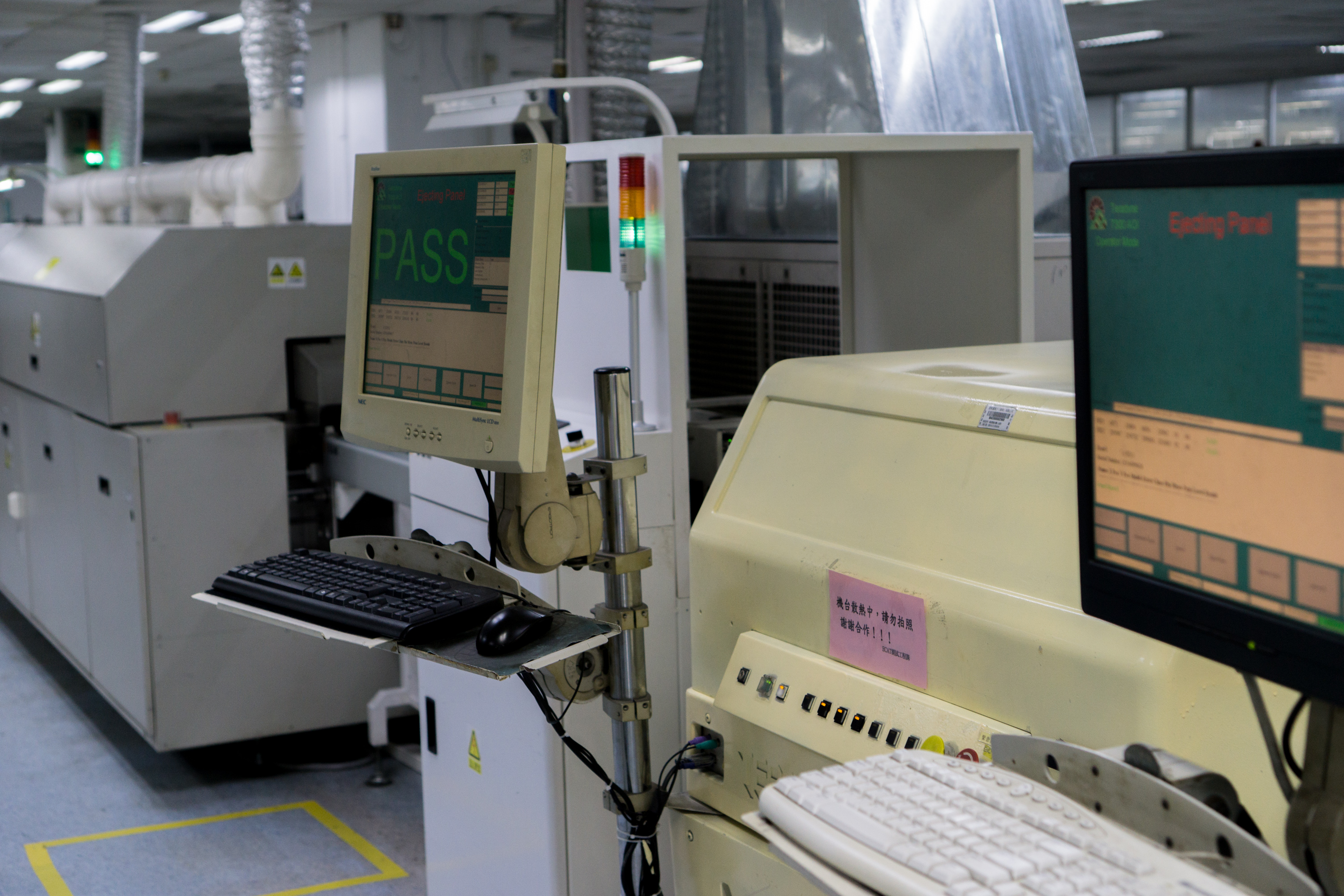
Quality control time! After the chips are placed, the boards run through a test to ensure everything is working properly.
According to MSI, the failure rate on the production line is about 4000 DPPMs (defect parts per million), or 0.4 percent.
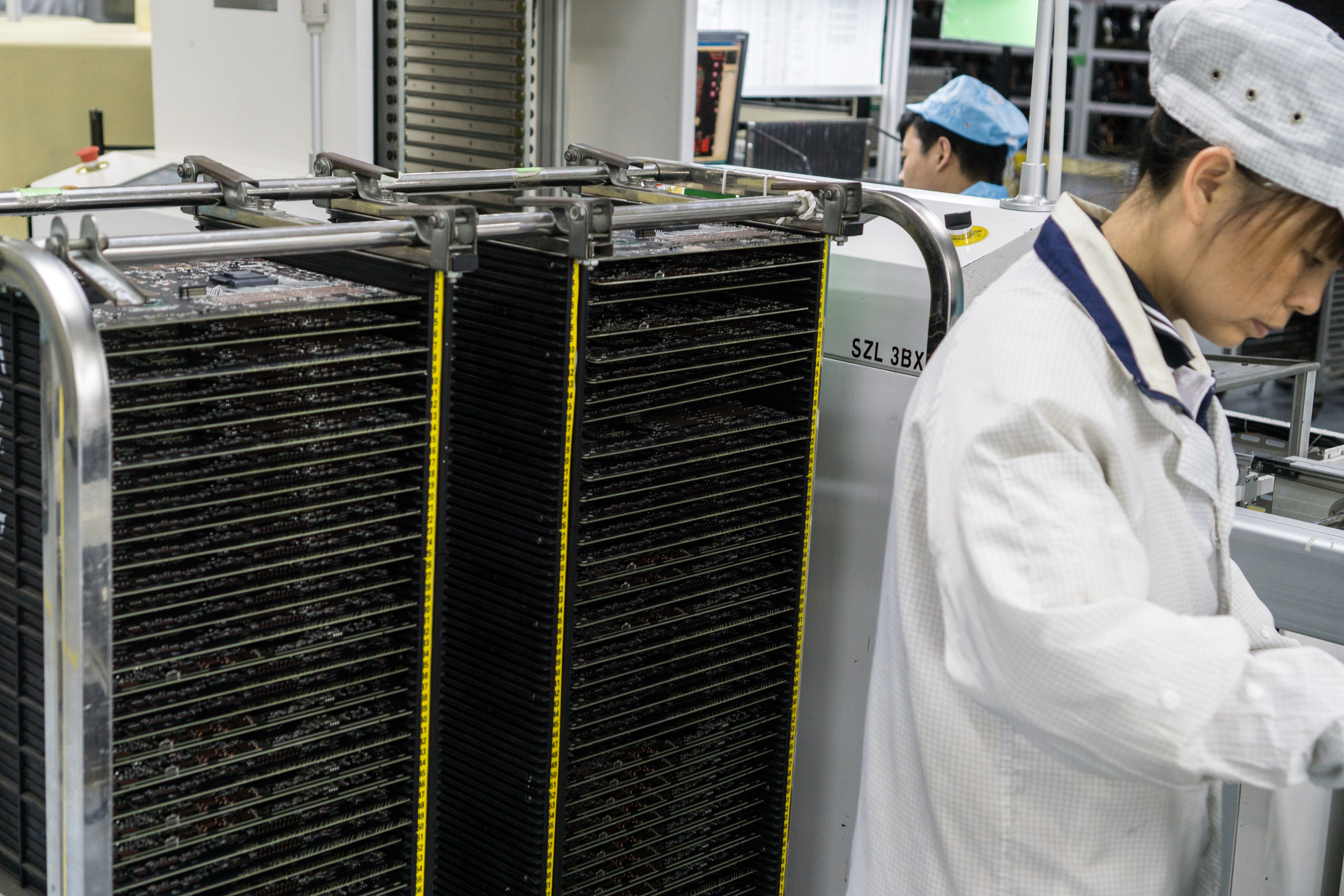
Motherboards on motherboards on motherboards. Here trays of in-progress boards await their turn to go onto the next stage of assembly, where more components will soon be added.
MSI's factory director explained that in recent years they've had to train employees to be be flexible and have wider skillsets in the past, because production styles are changing. High volume manufacturing used to be the norm, meaning they'd crank out thousands of a single product for days or even months. Now the manufacturing is far more mixed, meaning they change which boards are being produced frequently (sometimes as often as three times a day).
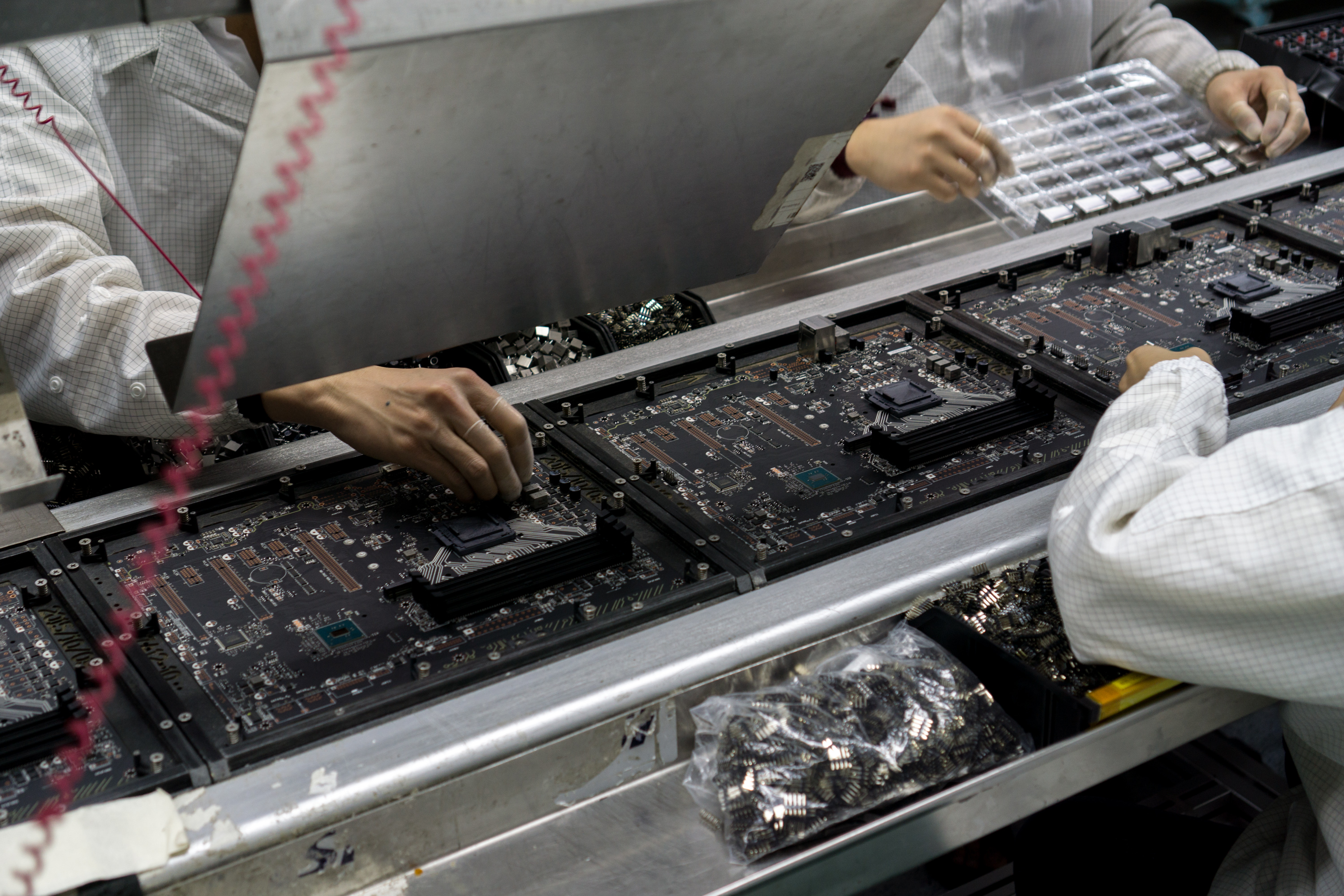
This stage of assembly is mostly manual. Workers on each side of a conveyor belt attach more parts to the motherboards, like the RAM slots and I/O connectors.
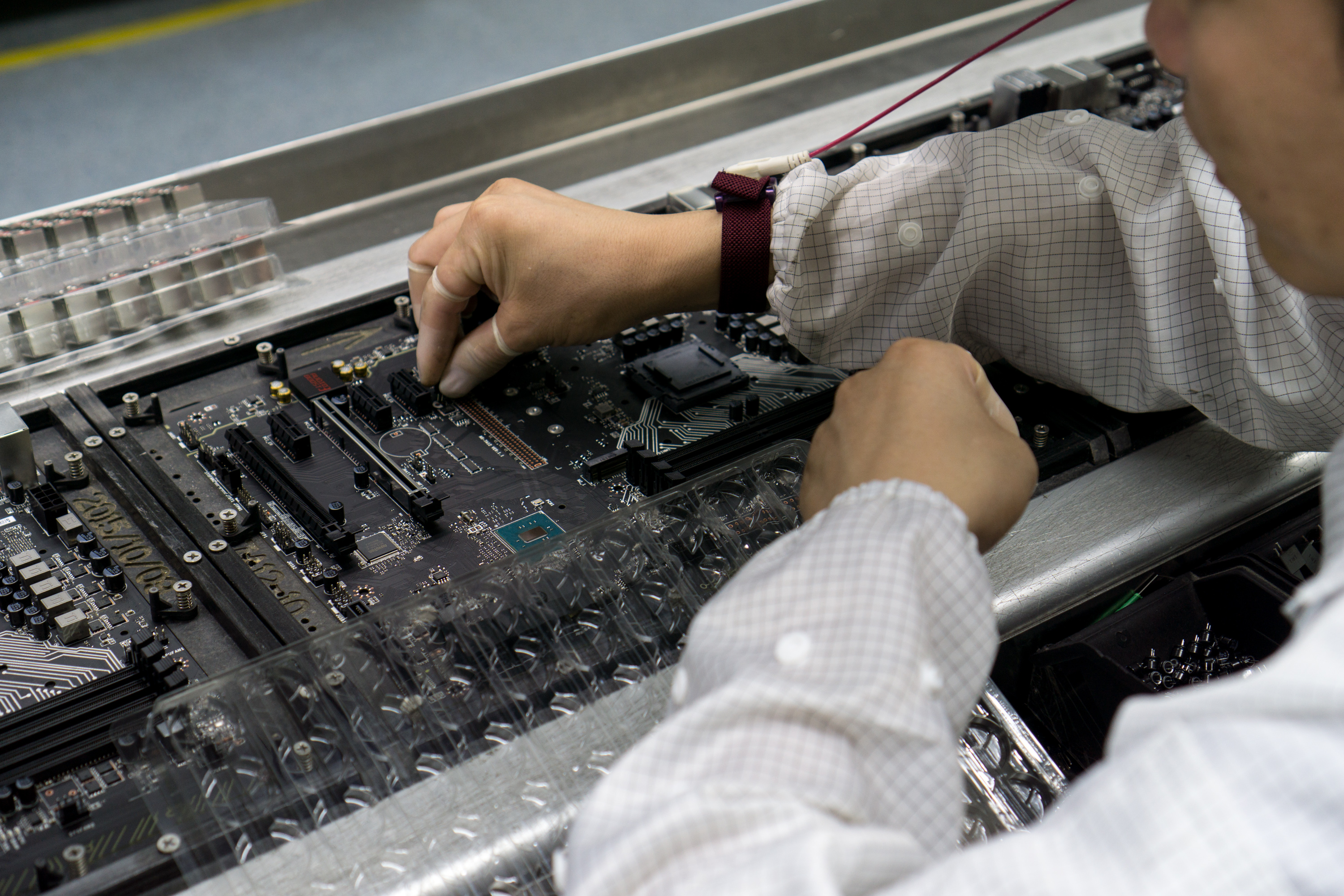
Further down the line, more workers add more components. Here the PCIe slots are being placed.
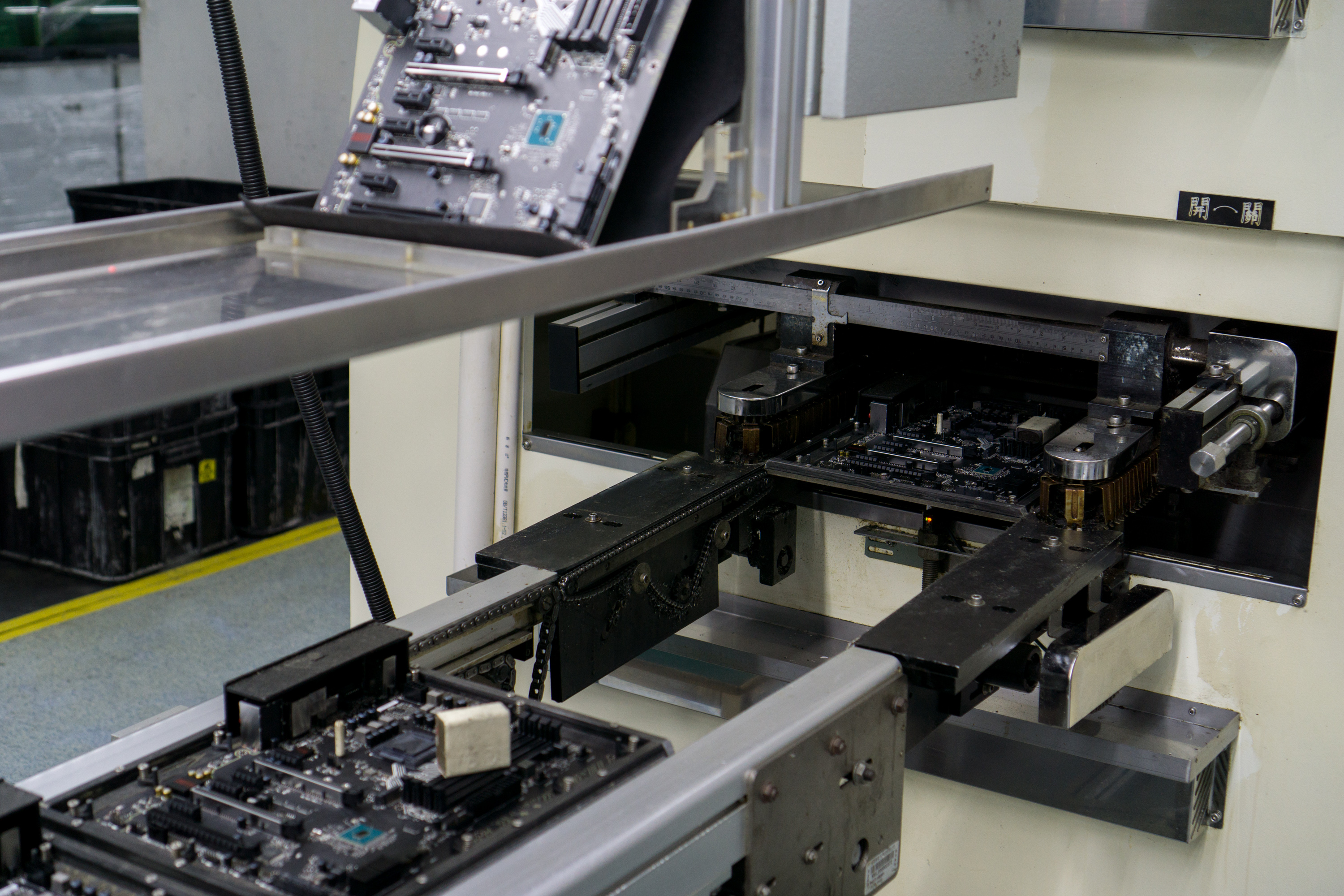
After those parts are added to the motherboards, they roll down the conveyor belt into another machine called a dual wave soldering system, which will secure everything to the board.
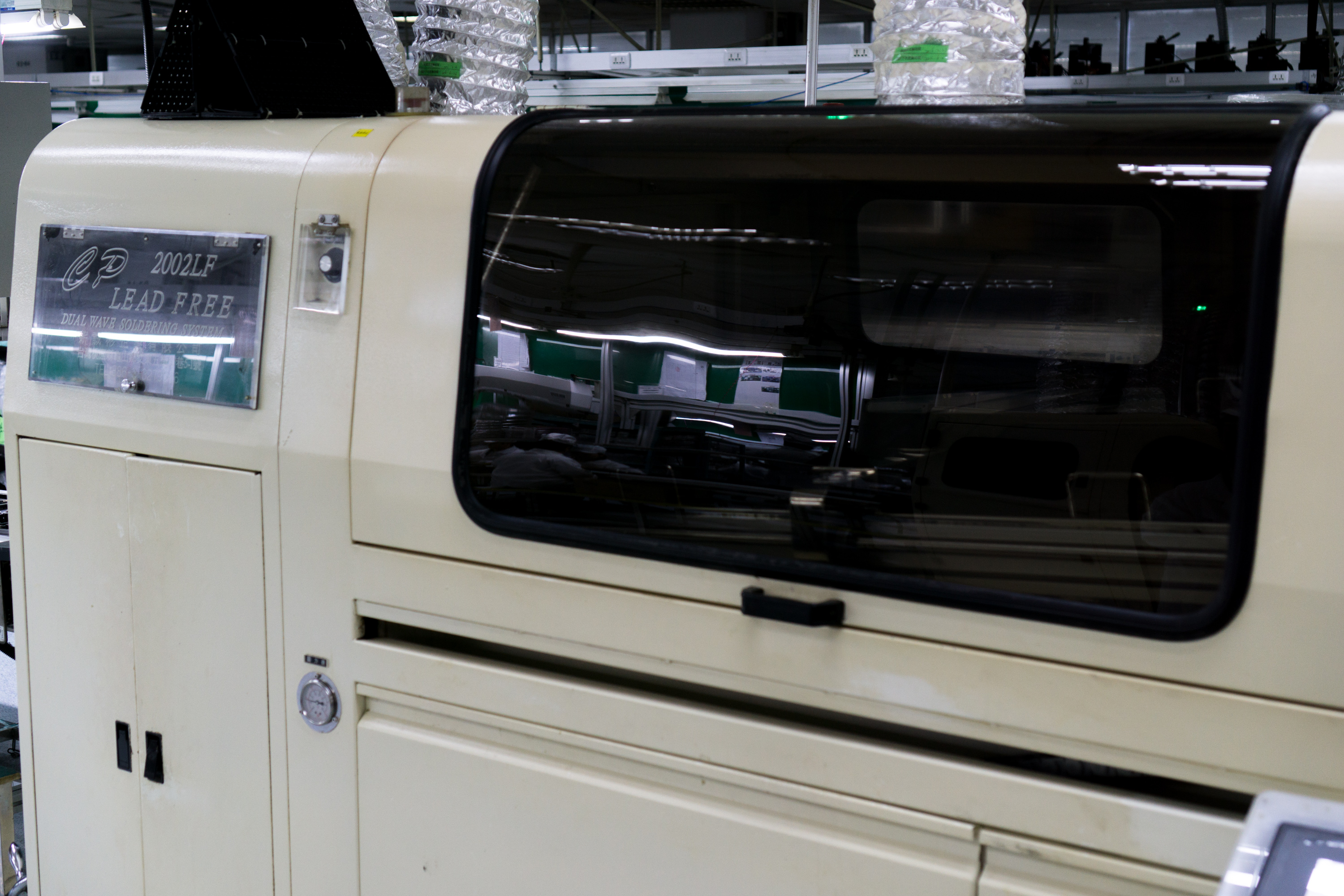
The dual wave soldering machine here will essentially cook the components into place, though that's a simplification of the soldering process. Here's an example video of a wave soldering machine in action.
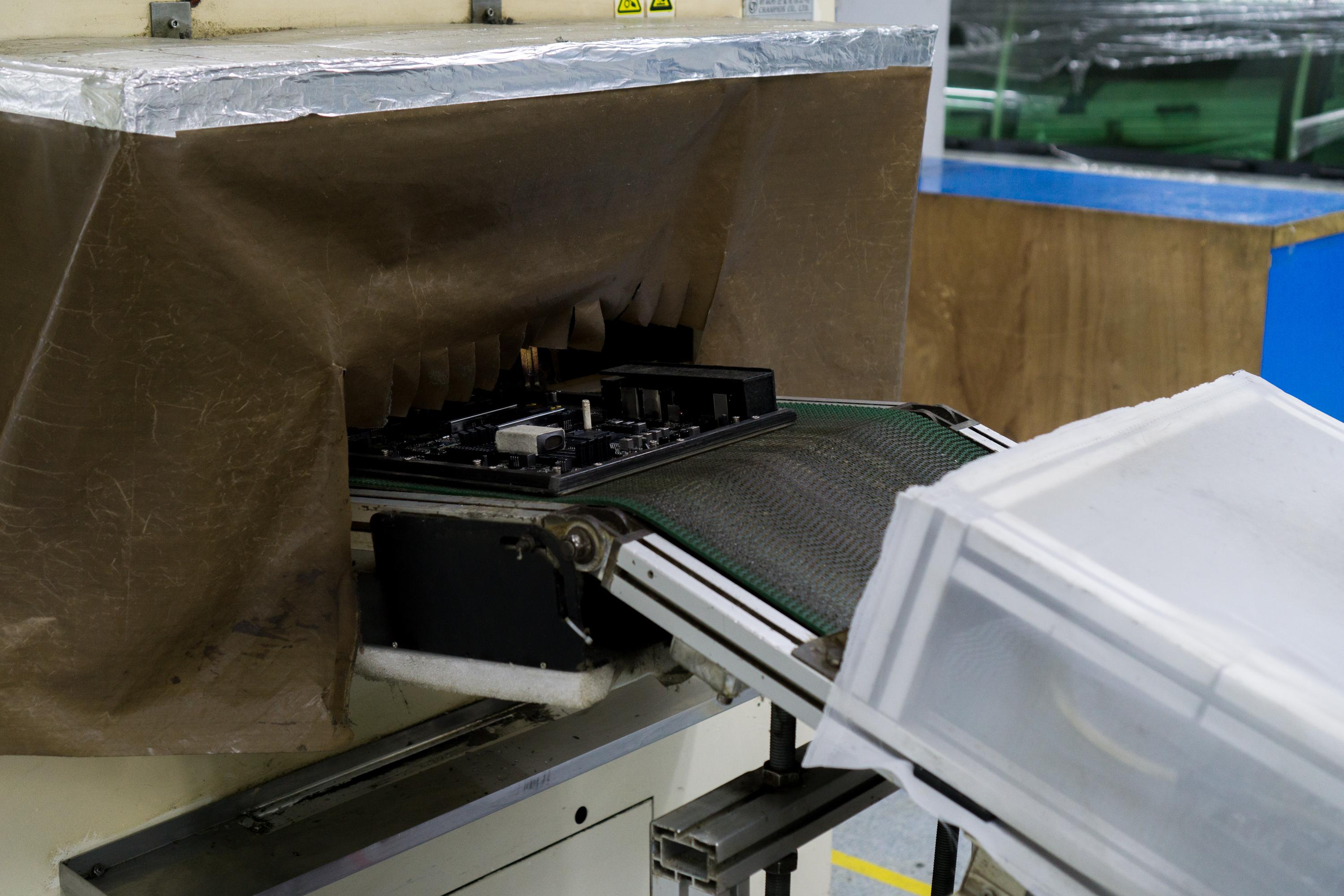
The boards leave the solder machine and head for the final stage of the assembly line, with just a few more components to be added.
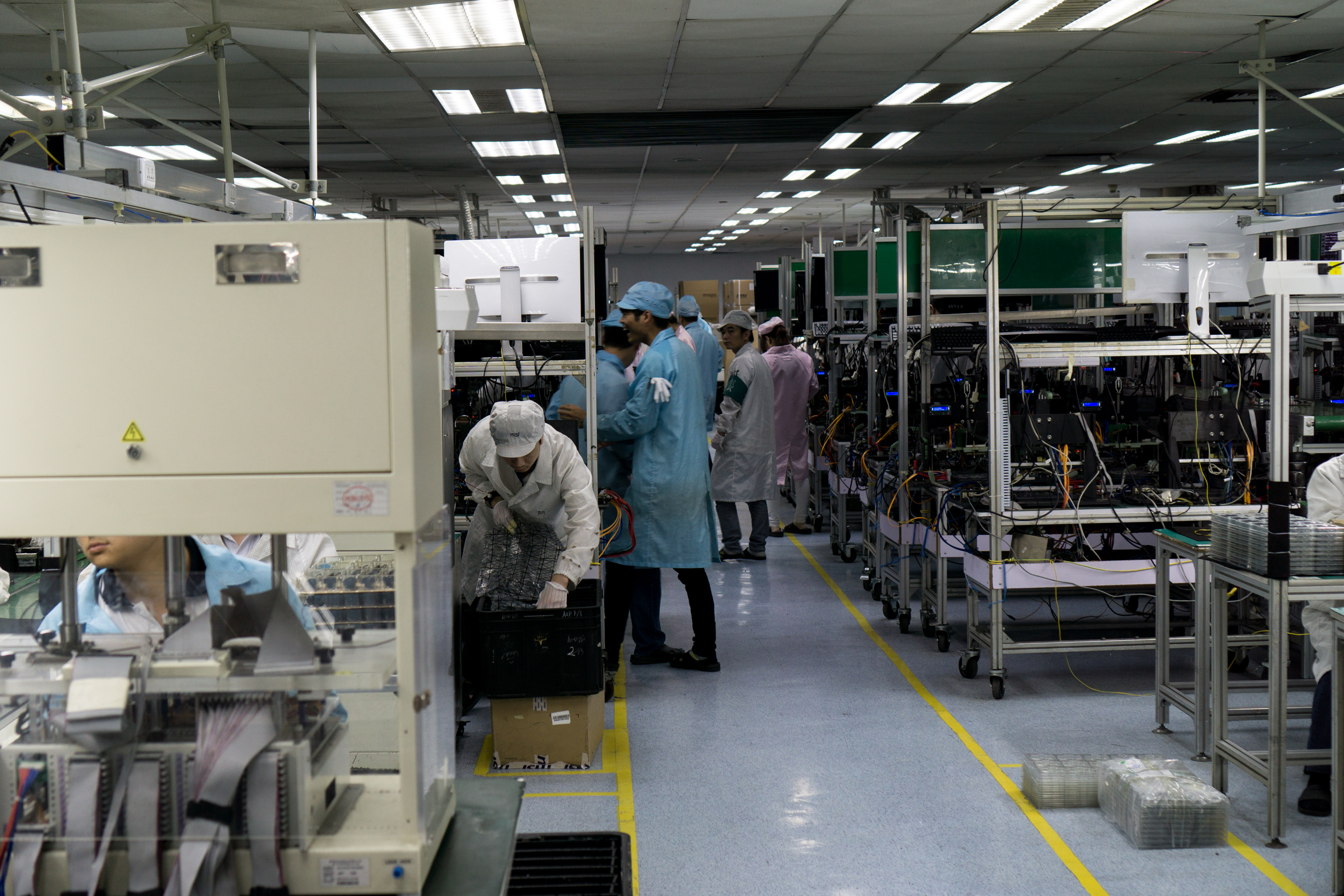
This shot is looking towards the back of the (very long) assembly room. The conveyor belt is to our left, and before boards are finished and ready to ship out, they have to go through a big testing area that checks for faults.
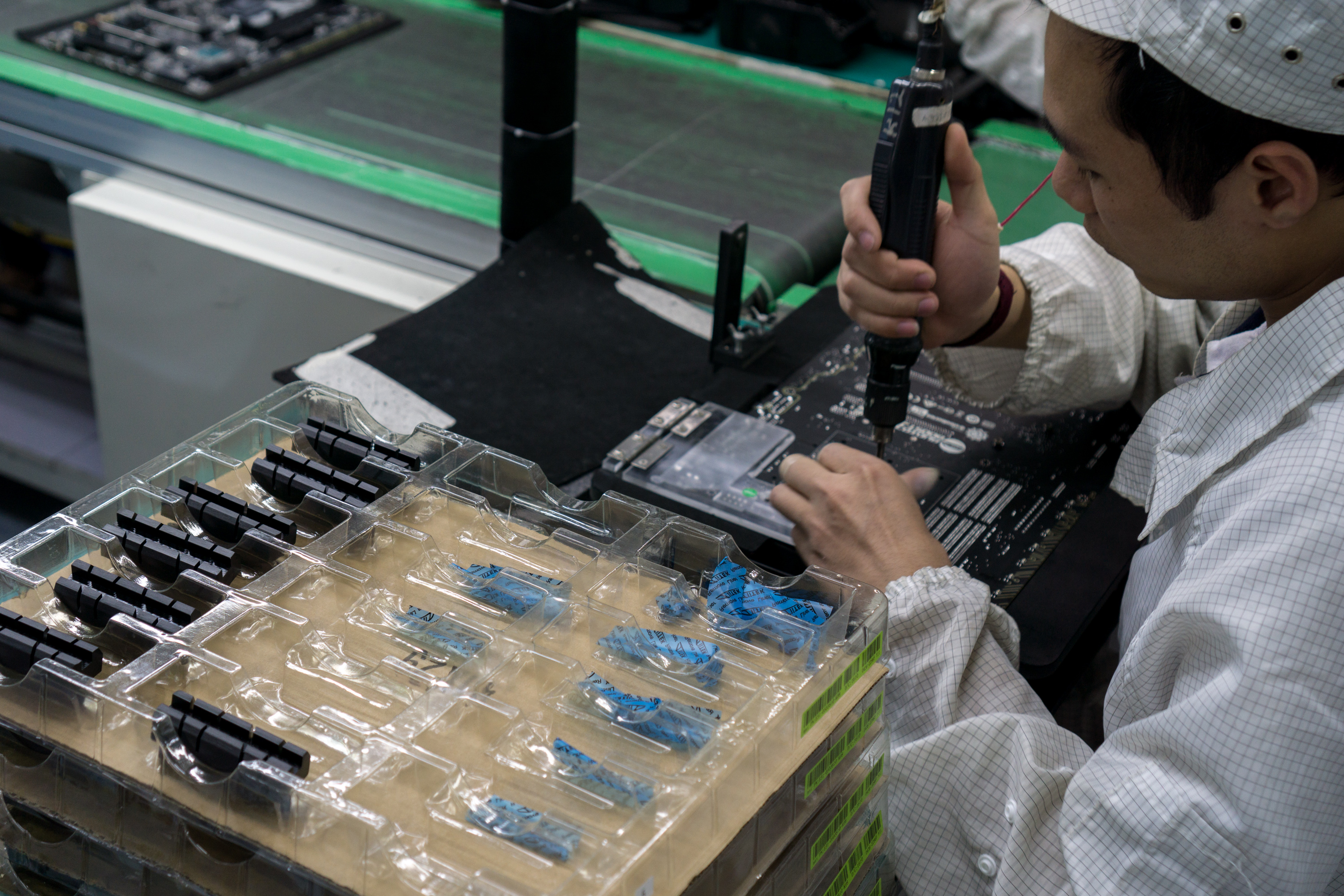
This worker uses an electric screwdriver to attach heatsinks to the motherboard chipsets.
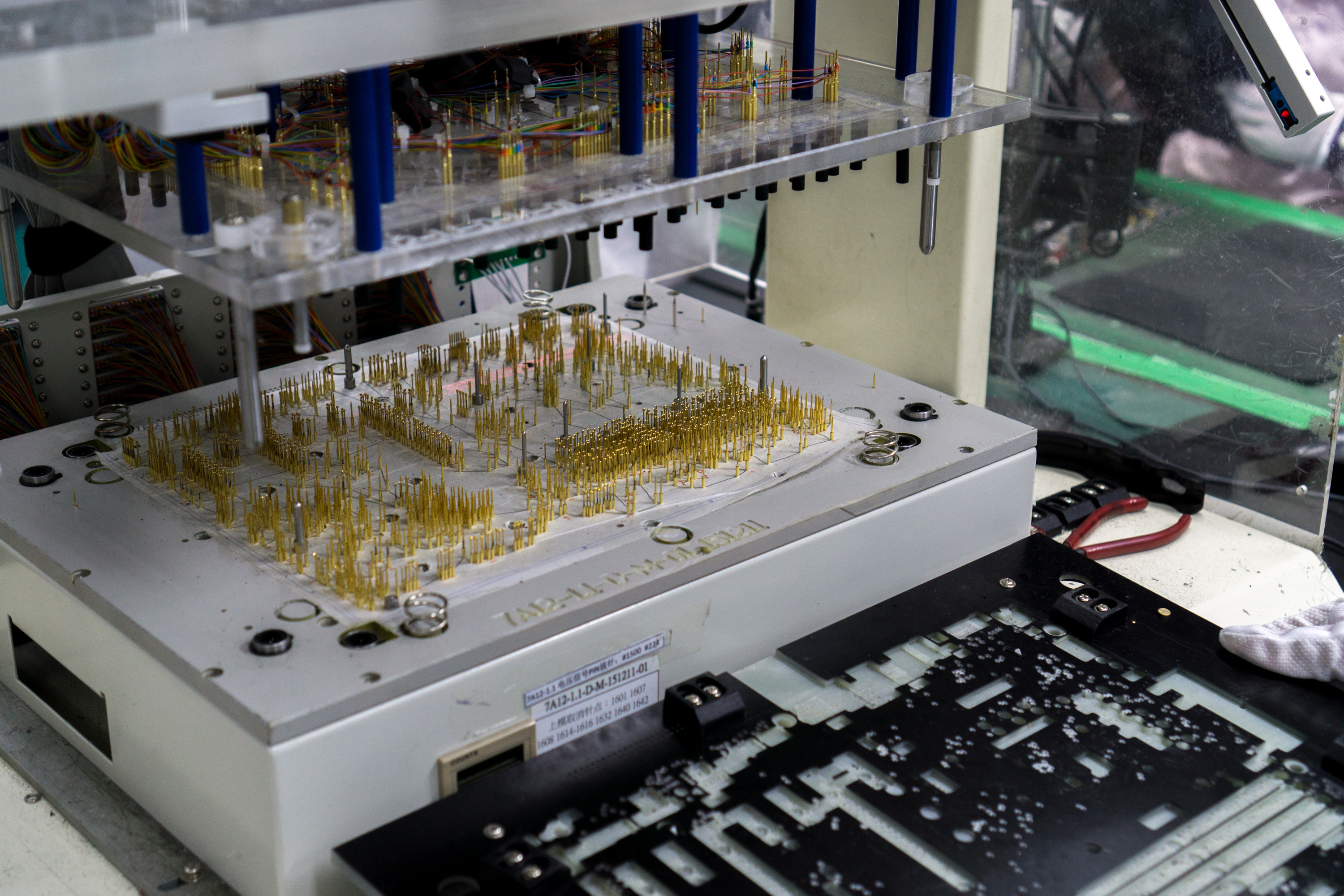
This machine uses hundreds of golden pins to connect to circuitry all across the motherboard. It's one step in the testing process to ensure everything is working as it should.
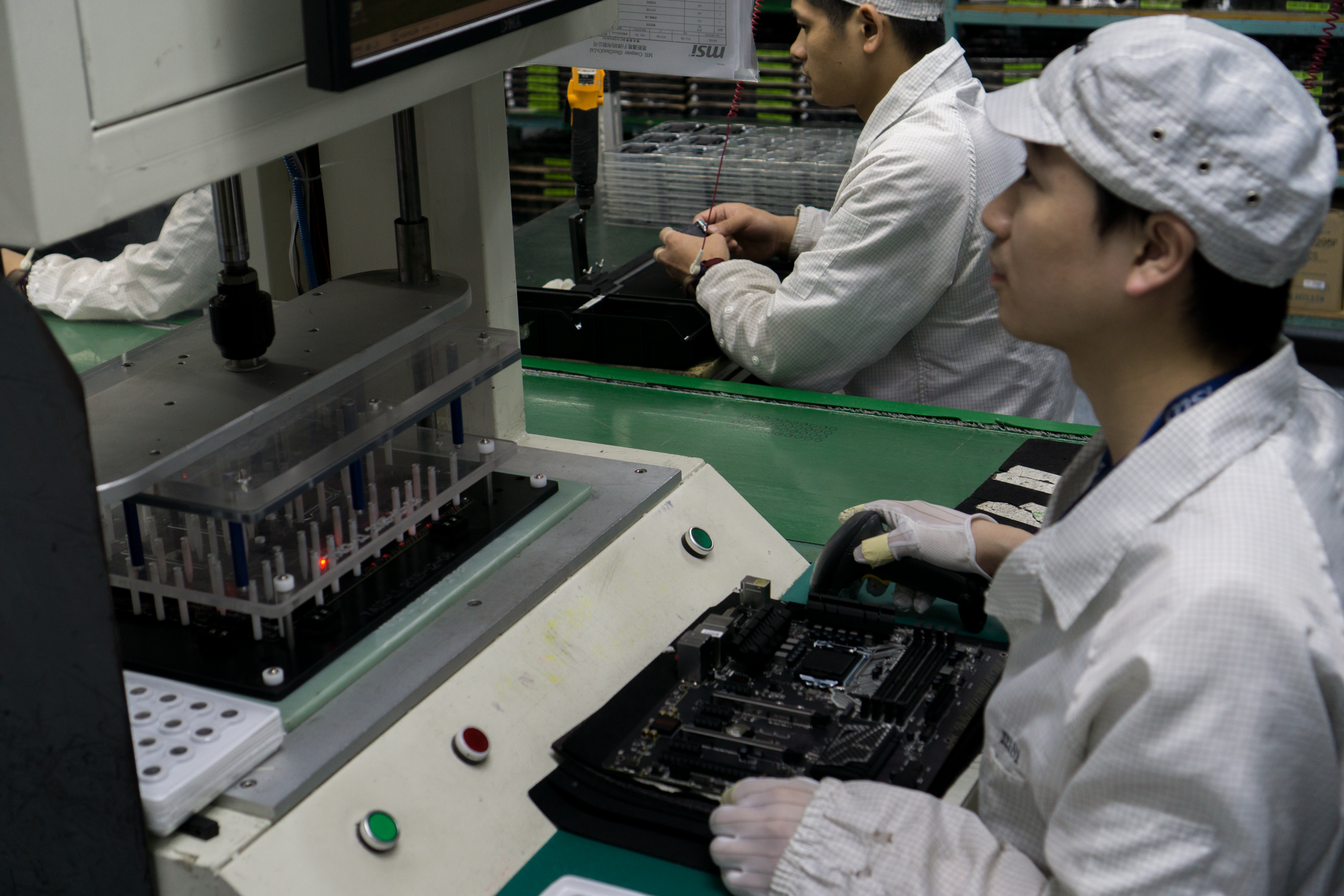
A worker references the computer screen above him to ensure the motherboard being tested checks out.
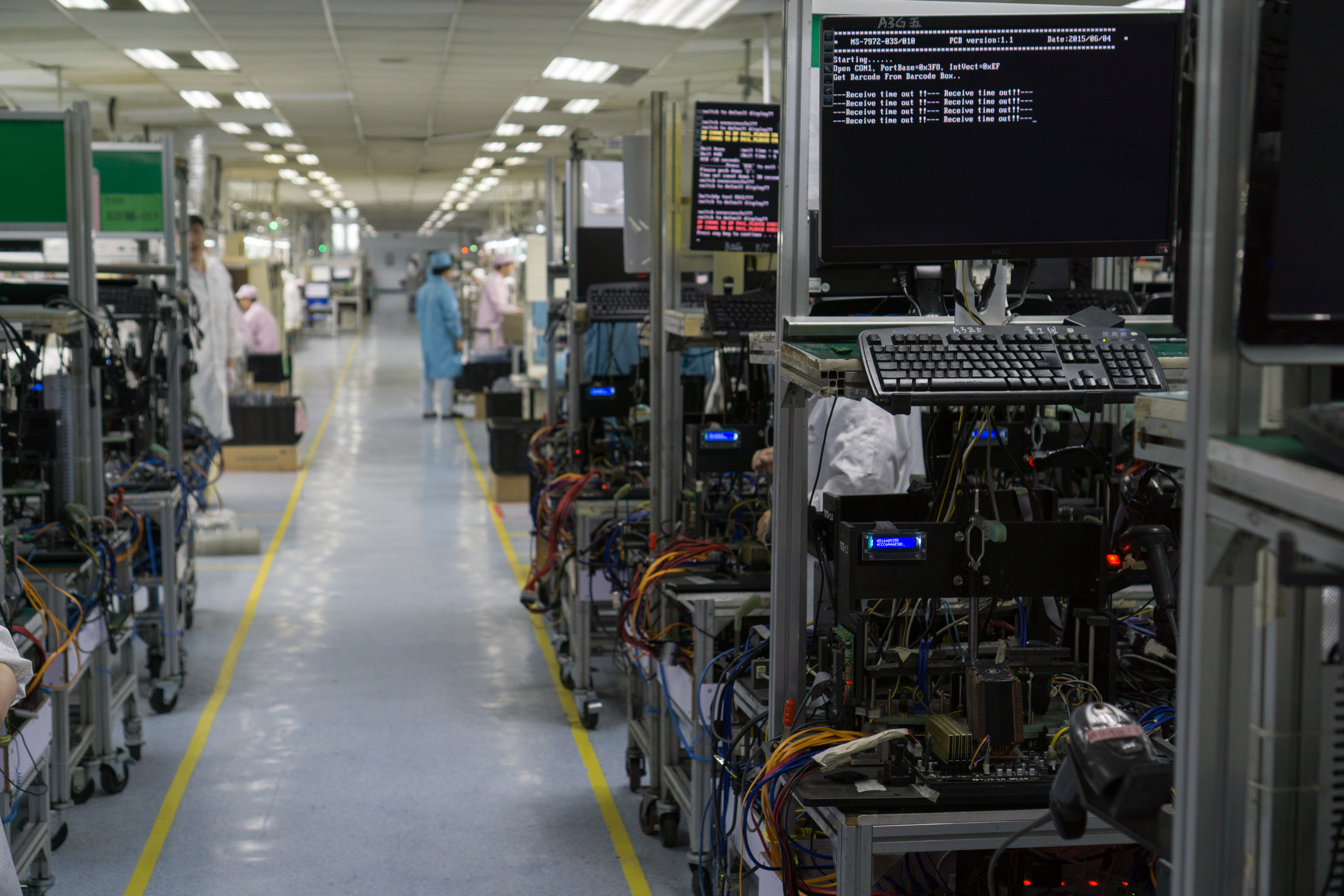
A look at the testing area. After motherboards go through the assembly process, they roll down the line to these stations, where workers plug in components and run diagnostics to ensure there are no issues.
In recent years, MSI has developed some of its own testing tools and procedures to improve its production process. This has helped them test for a wider range of problems and feed the data collected back into R&D, engineering, and operators on the assembly line.
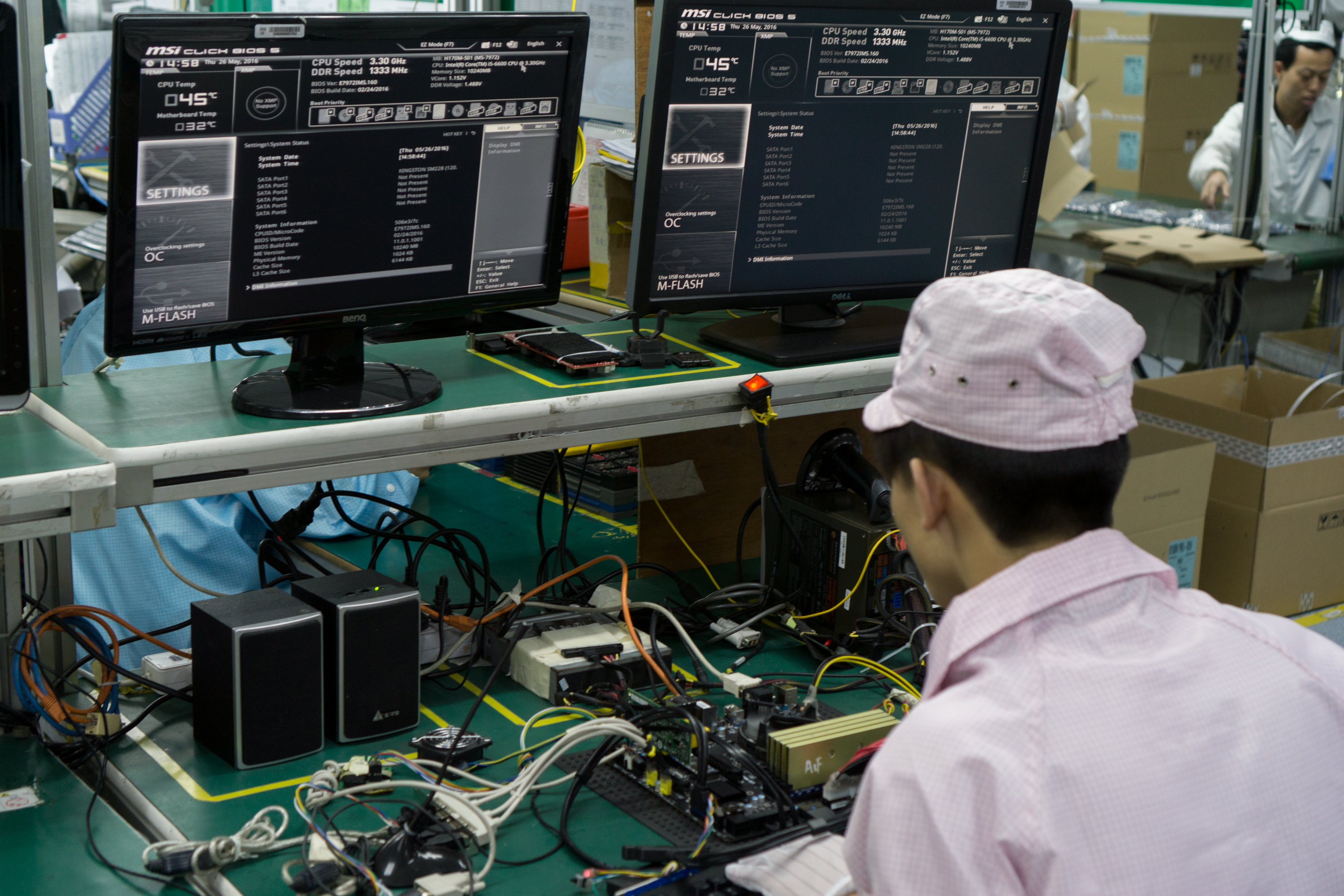
This motherboard is being tested as if it was a fully built PC. Power is attached, RAM and a CPU are added, and the worker books to the BIOs to see that all is well.
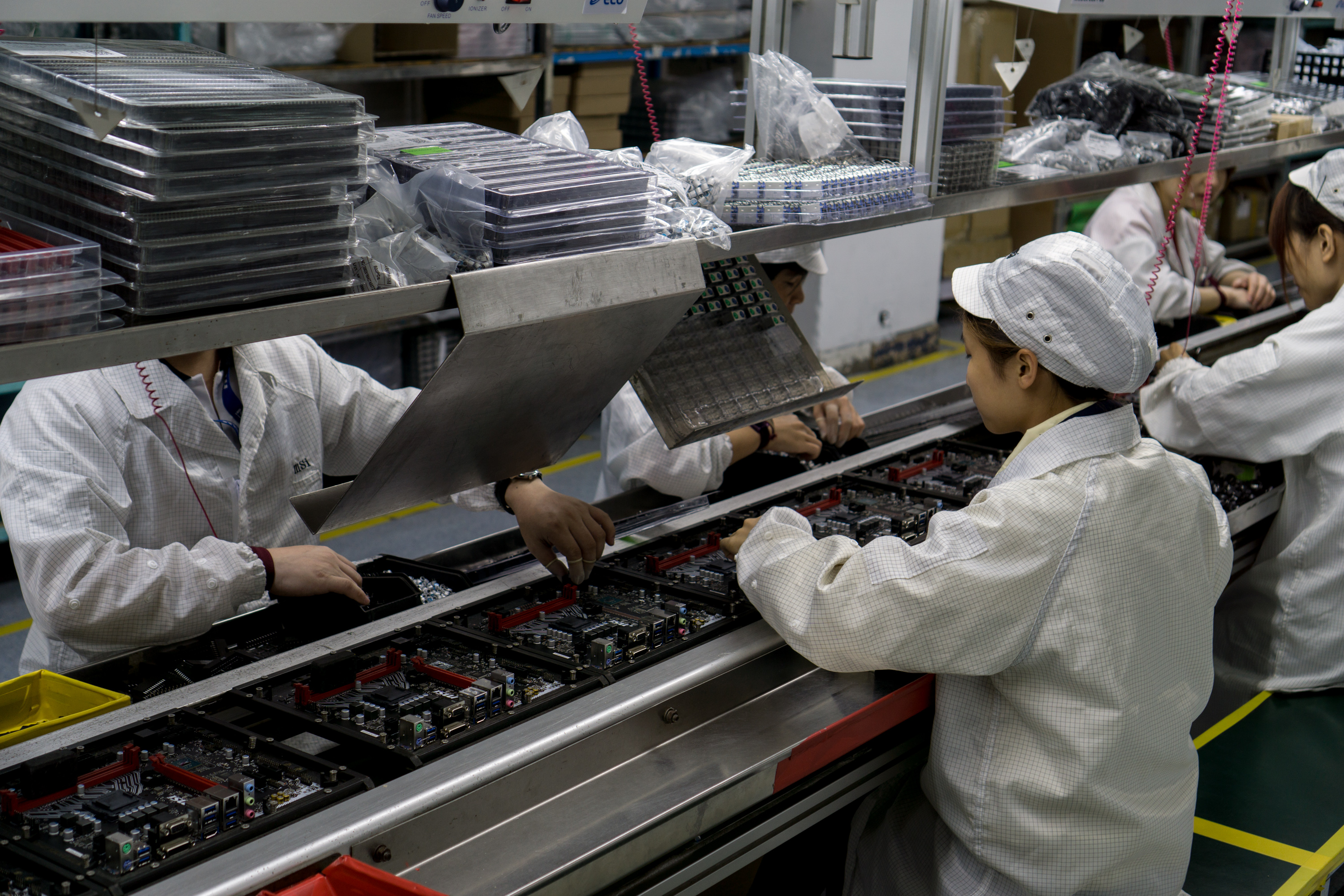
Another look at the assembly line running parallel to the one I walked down. These boards are in the final stages of components being added.
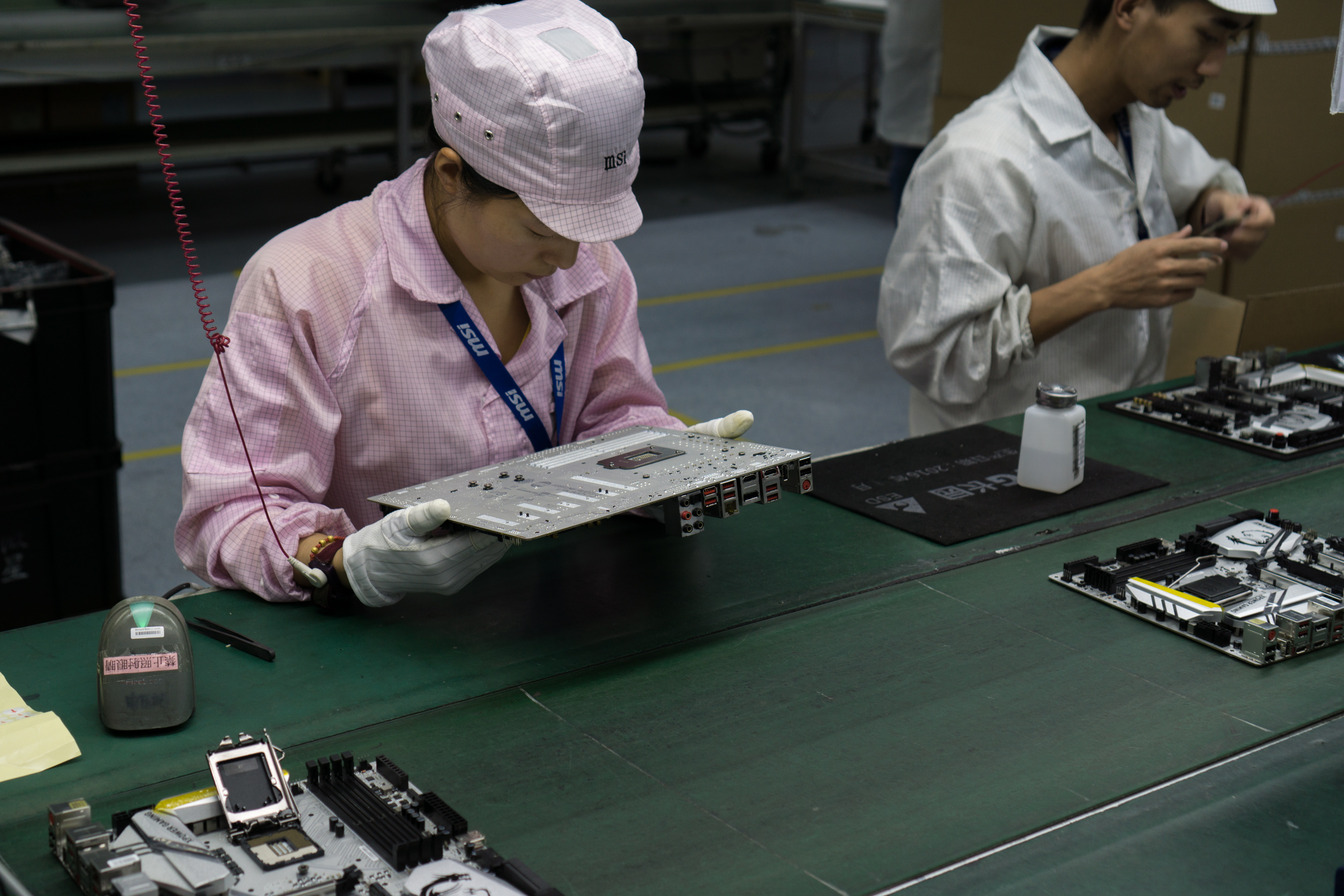
A worker checks the back side of a motherboard to ensure its tracings and components are properly in place before it's packaged up for shipping.
Some inspections are best done by the human eye, but others require machines. MSI's factory director told me that some parts are now so small, humans can't inspect them, so they've designed their own in-house inspection machines. The CPU socket, for example, has more than 2000 tiny pins.
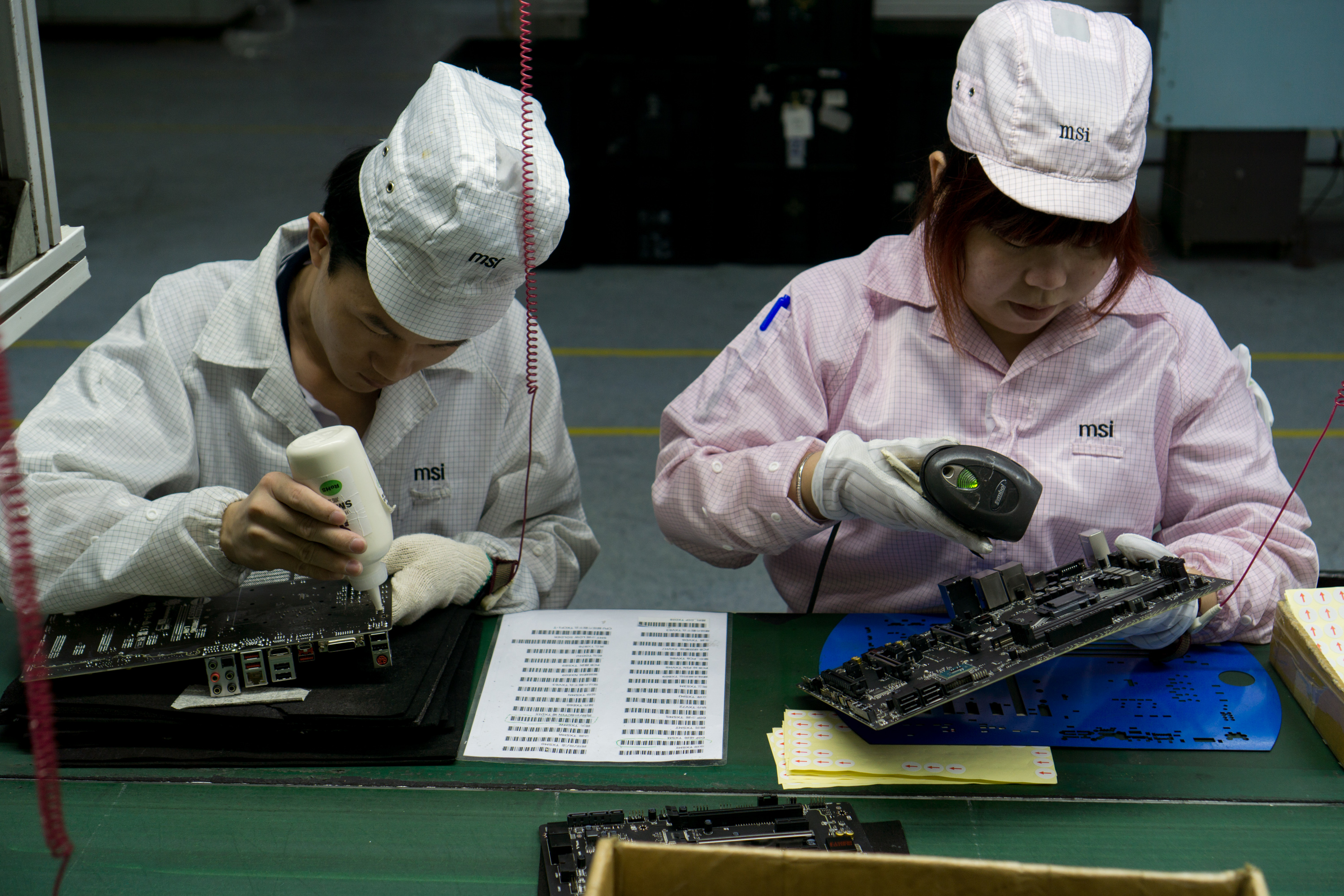
Each motherboard gets a barcode and is checked off the list. No lost boards!
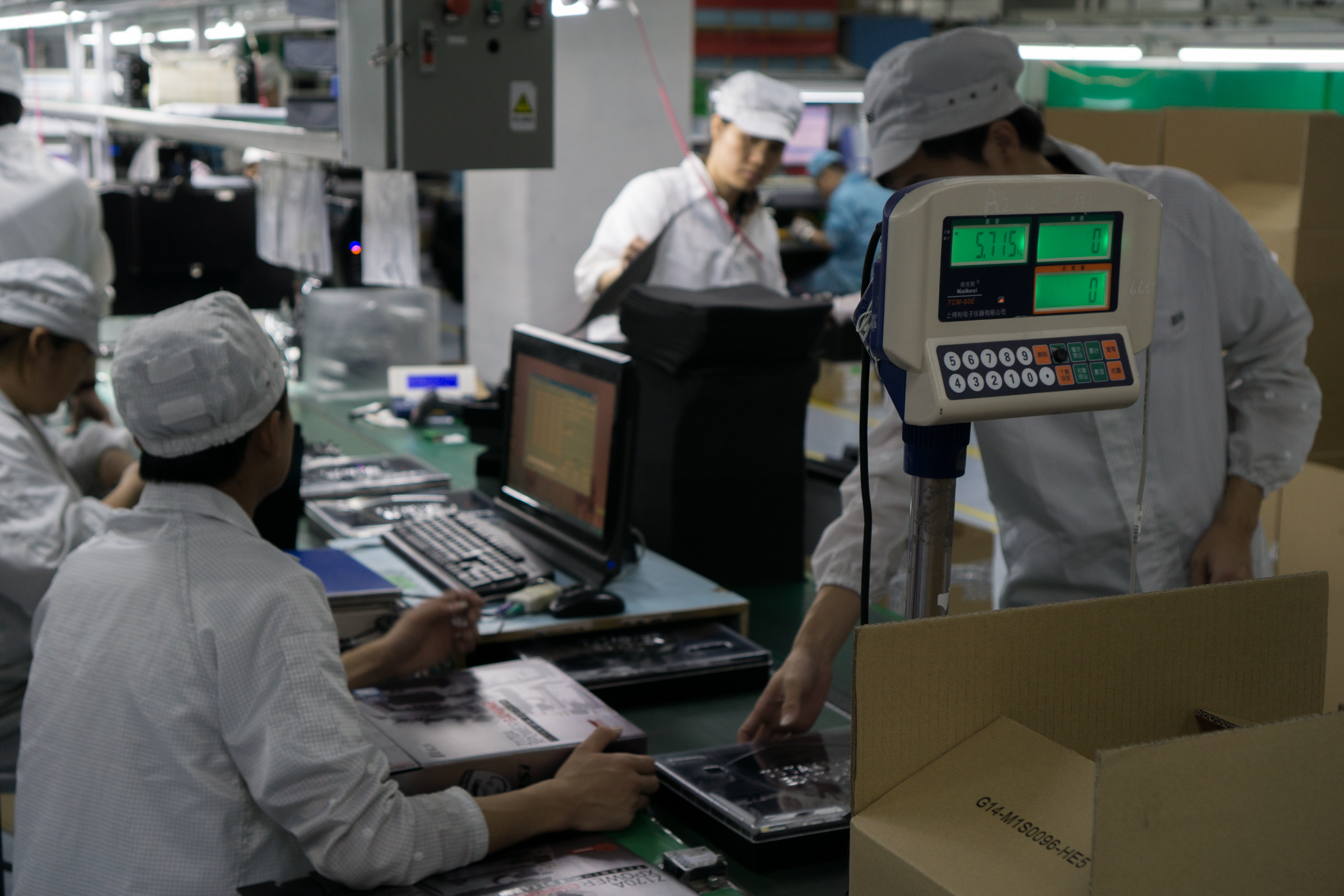
After motherboards are placed in their packaging, several will be stacked into a larger box for shipping. But before this goes out, it's put on a scale to ensure the weight is exactly as it should be, and nothing is missing.
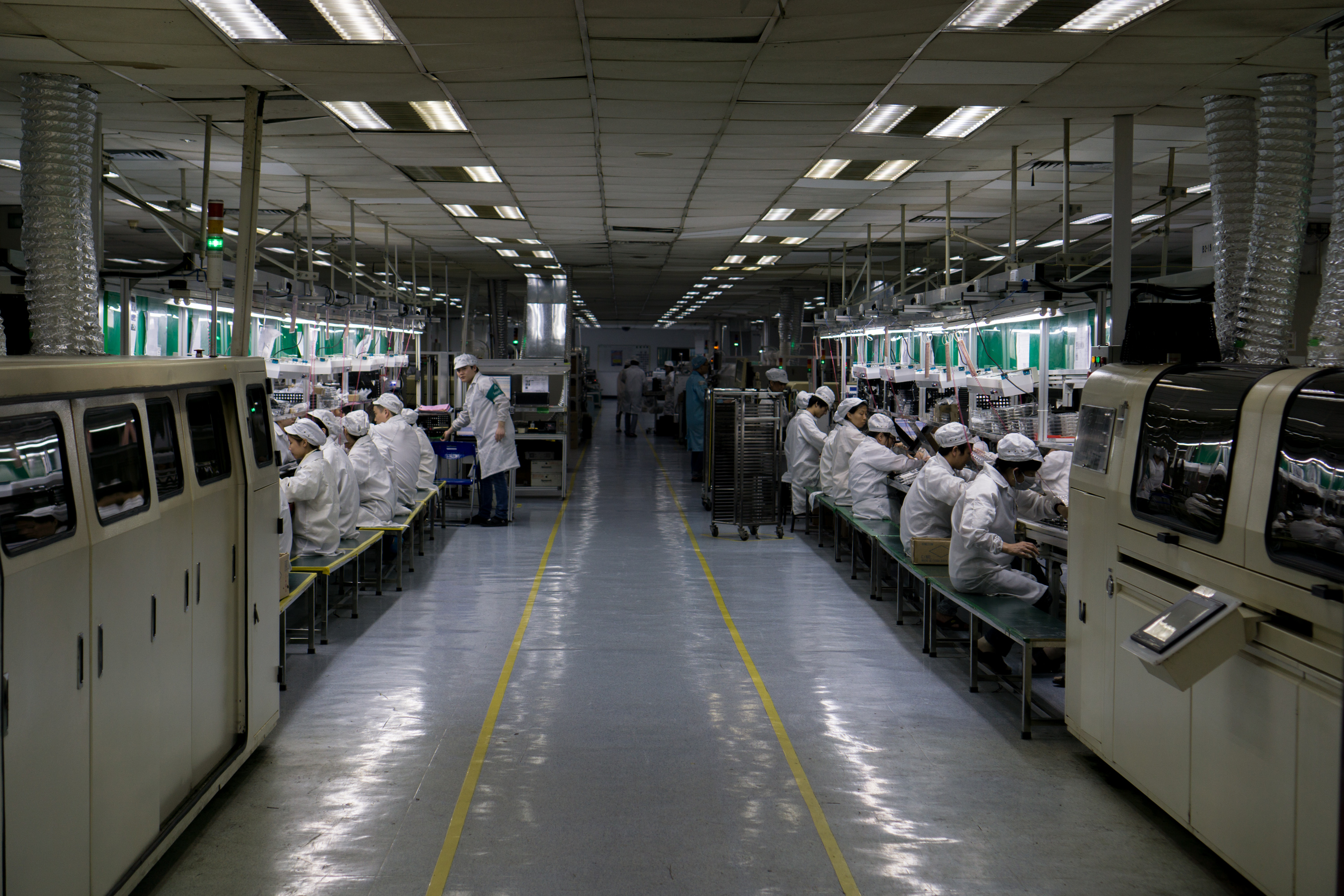
And that's how motherboards are made at MSI. Workers here have ten hour shifts, with two hour production breaks for lunch and dinner. That's a day at MSI's factory, which produces around 60,000 motherboards every single day, and another 30,000 graphics cards.
But wer're not done with our tour yet: in the next 12 slides, hardware EIC Tuan Nguyen takes us through MSI's HQ in Taiwan.
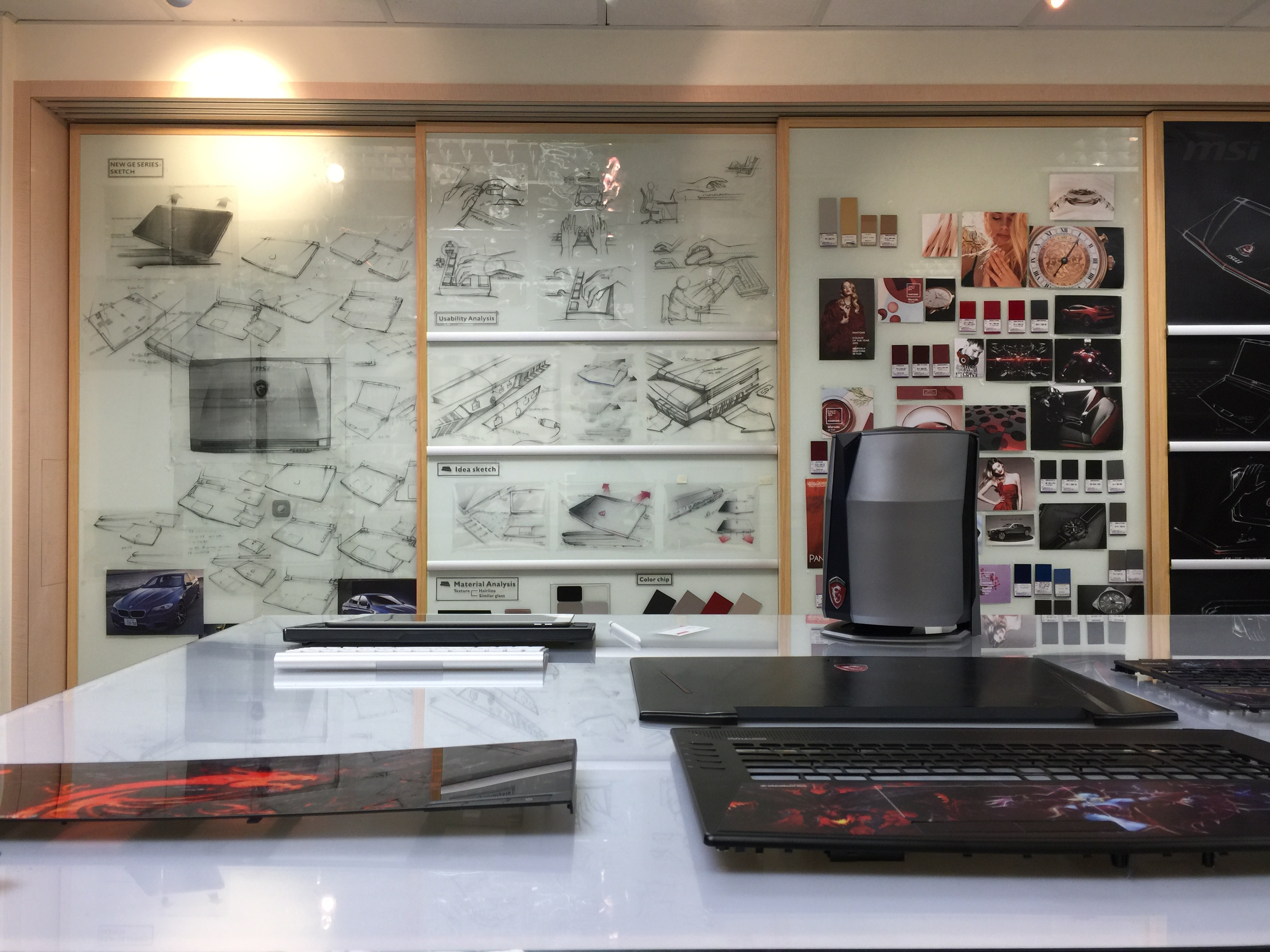
The room above is where many of MSI's products are designed. Concepts, prototypes, and refinements are all sketched out. The product design team goes through many iterations before arriving at a final design. Materials and colors are selected here.
There are large whiteboards all over the room for attaching various inspirational designs and clippings. Everything from car photos, to jewelry, to houses are put on the board. The design team then uses the design collage to create an initial design.
The white board doors slide open to reveal a treasure trove of mockups and prototype designs that didn't make the cut. Unfortunately, we weren't allowed to snap photos of the early prototypes.
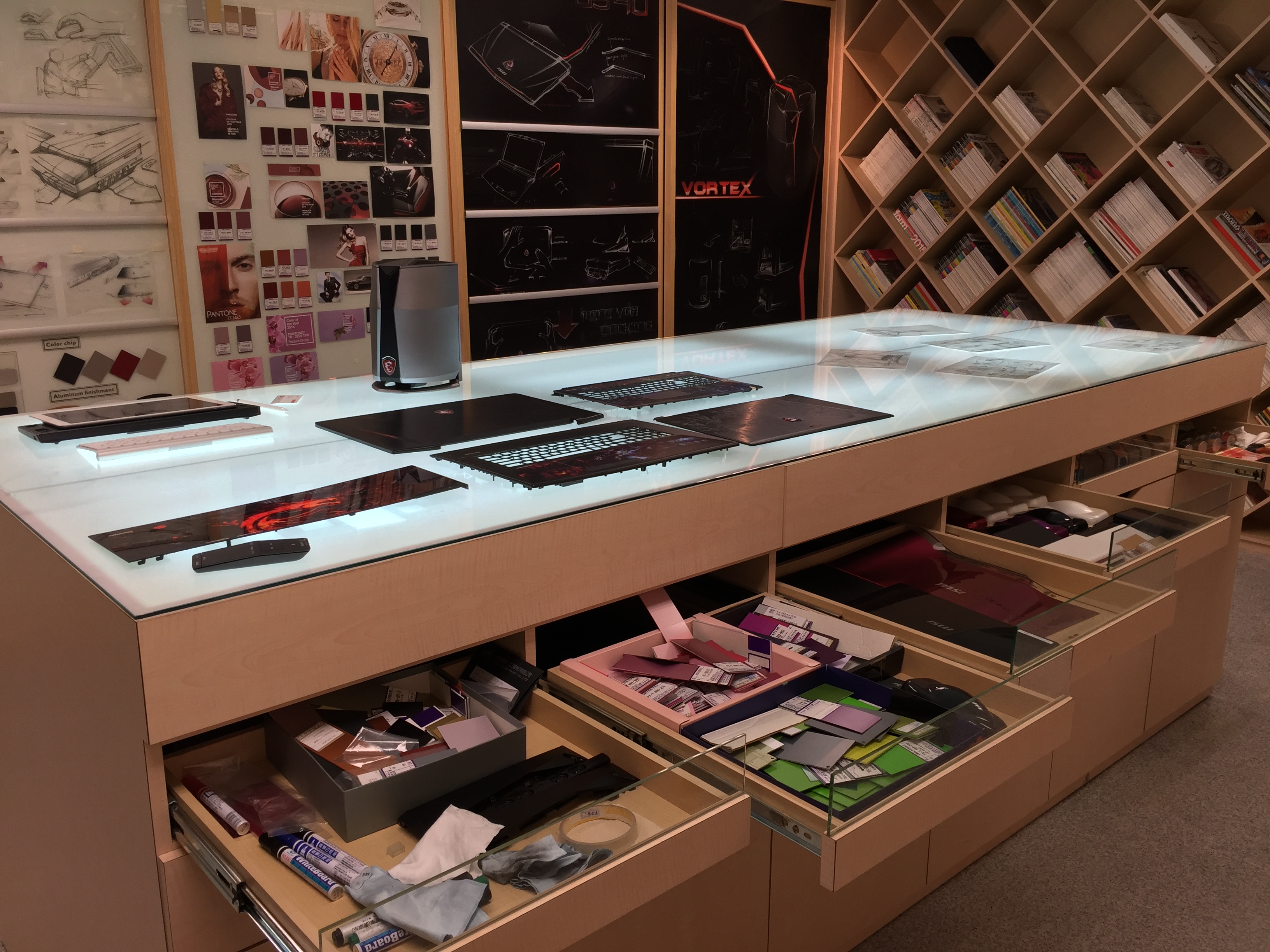
There's a center island in the middle of the room that contains all sorts of goodies. Material samples, 3D printed mockups, paint color samples, and more. At the far end, there's a shelf of reference design books to use for inspiration.
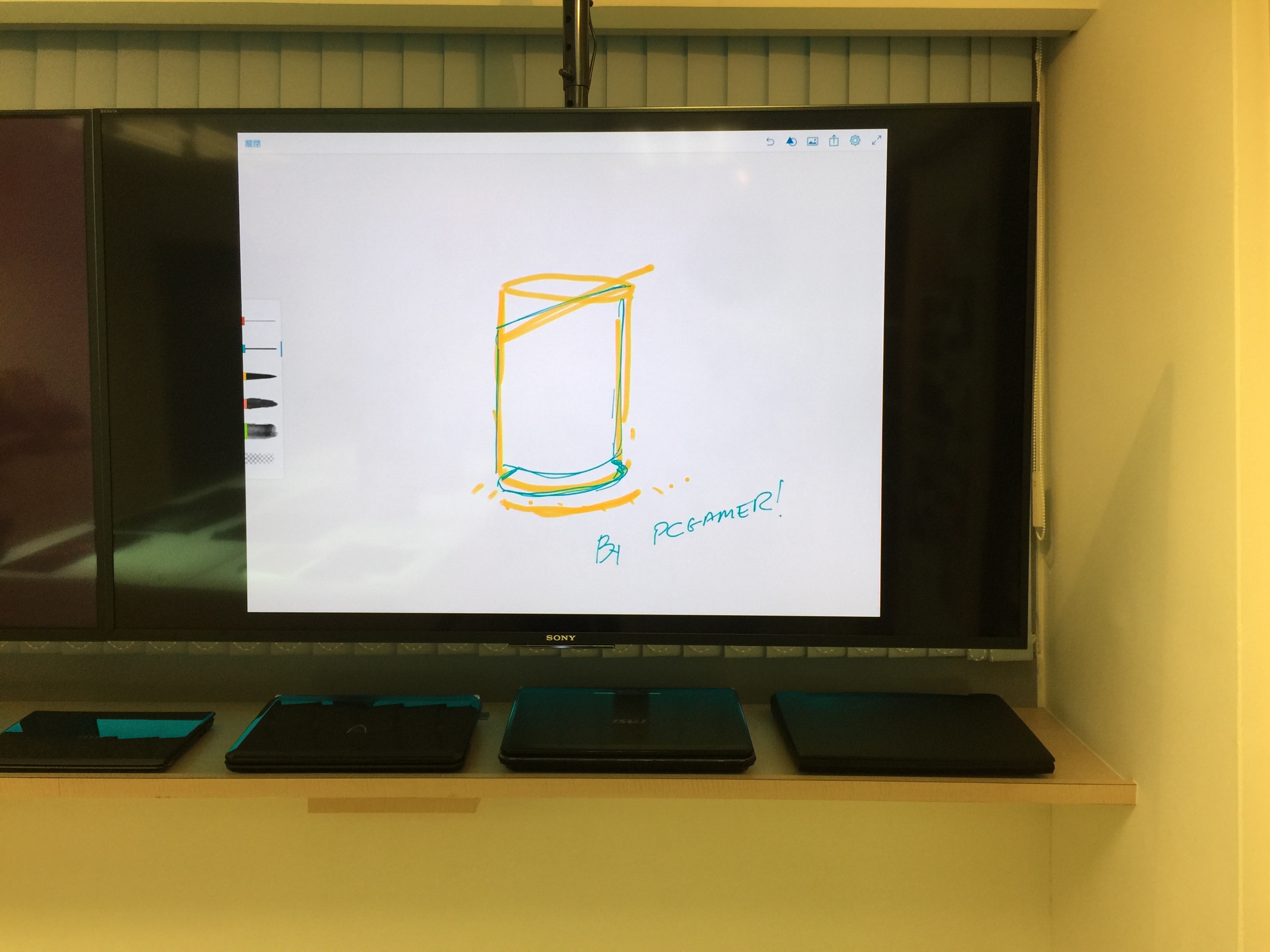
We had a debate with several folks from MSI's design team on the finished design of its Vortex PC, and decided to live-sketch what we thought would be a cooler mockup. Unfortunately, they disagreed that our design was better.
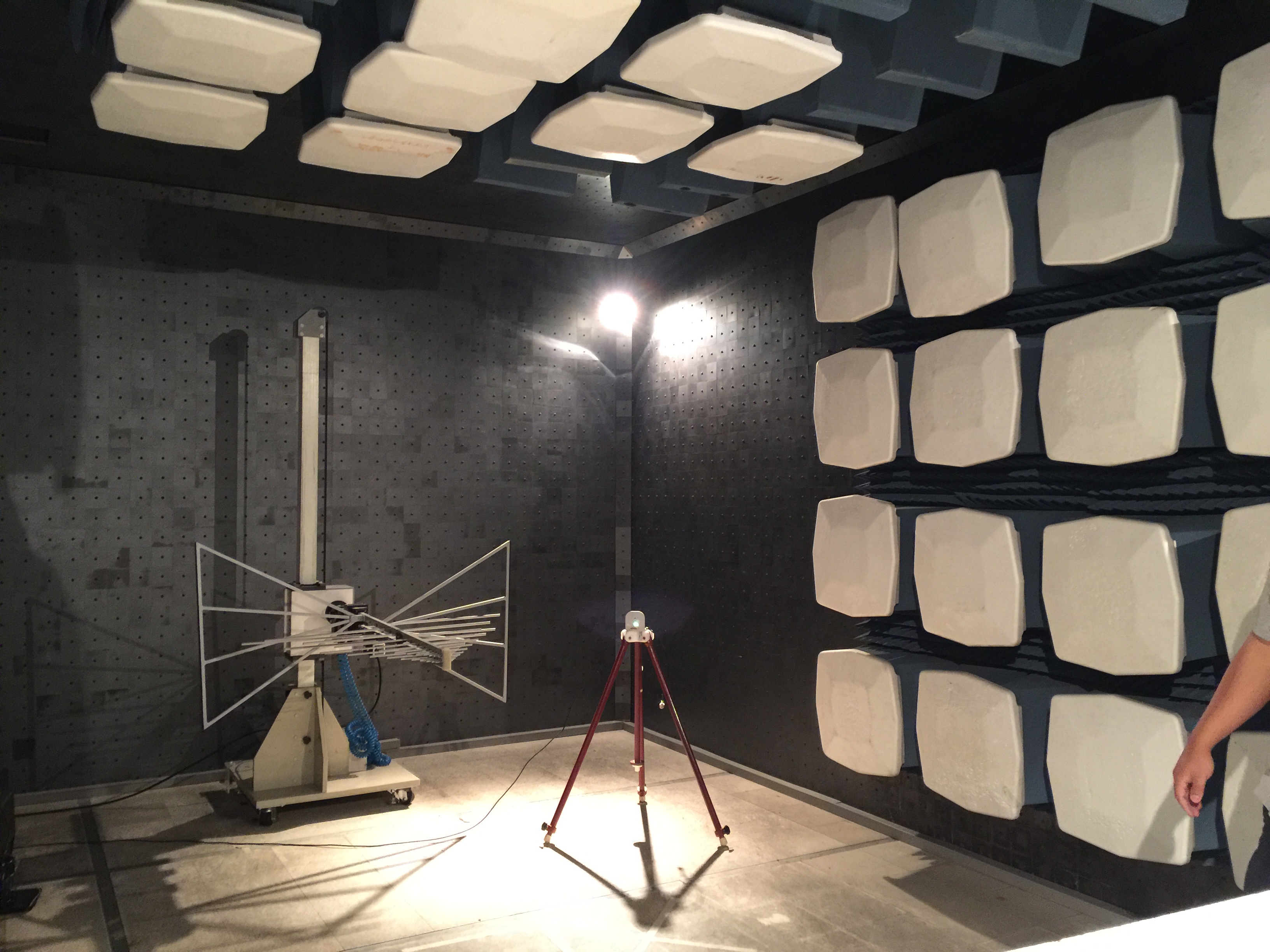
Here's one of MSI's many anechoic chambers. This one in particular plays hosts to testing of wireless devices. The room is completely void of outside radio frequencies. Step into here, and the signal on your mobile phone drops off completely. If you're ever stuck in here, there's no chance of dialing for help.
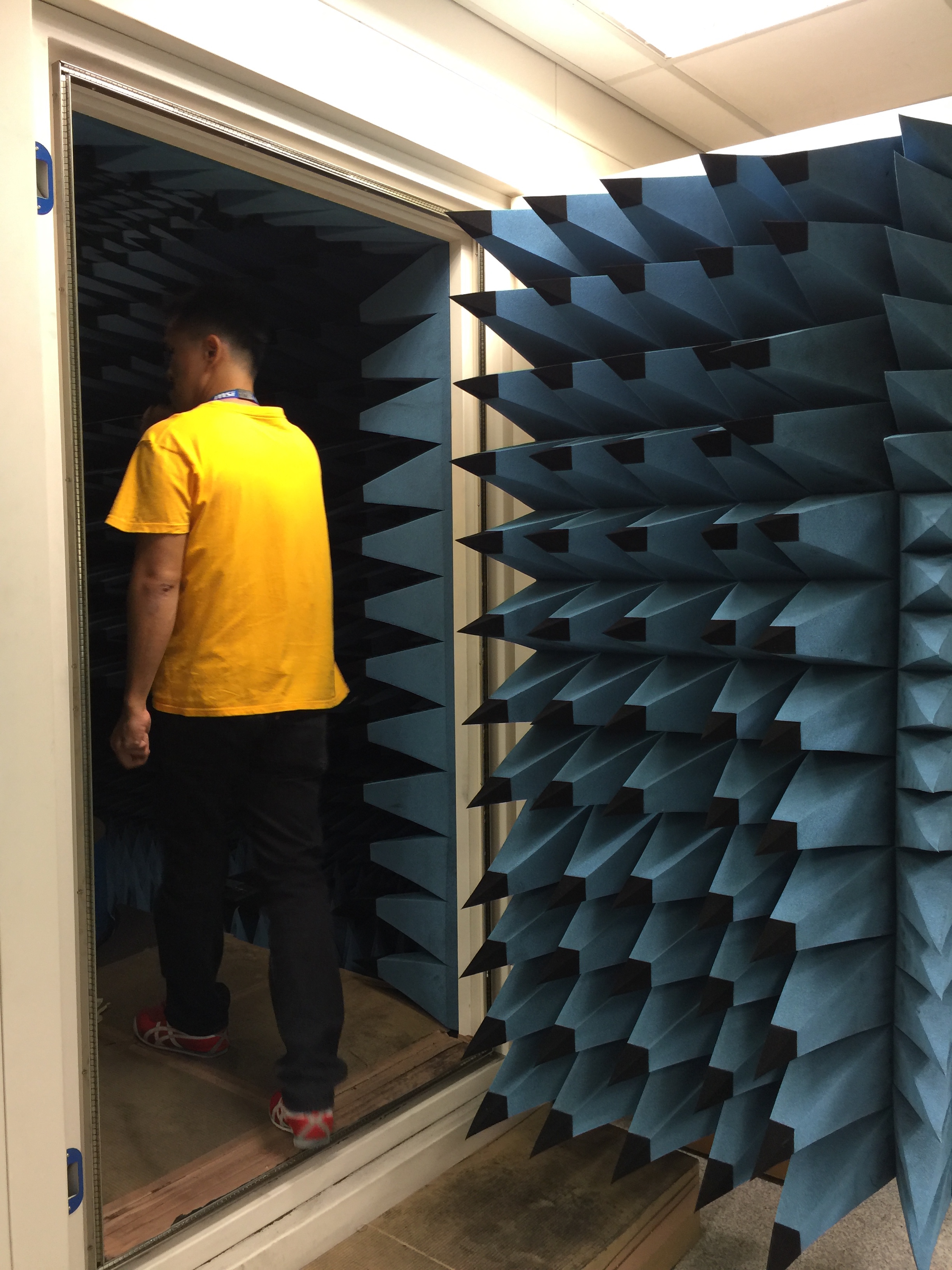
One of MSI's engineers walk into another anechoic chamber to demonstrate just how large they can be. In fact, as big as the one in the above photo was, there are anechoic chambers around the world that are much larger.
We were told not to touch the special foam sound insulation. Apparently, there's a special coating on them that is a bit hazardous for humans, especially if you forget and eat food with your hands or rub your eyes. We touched them anyway and the blue coating feels like a fine dust.
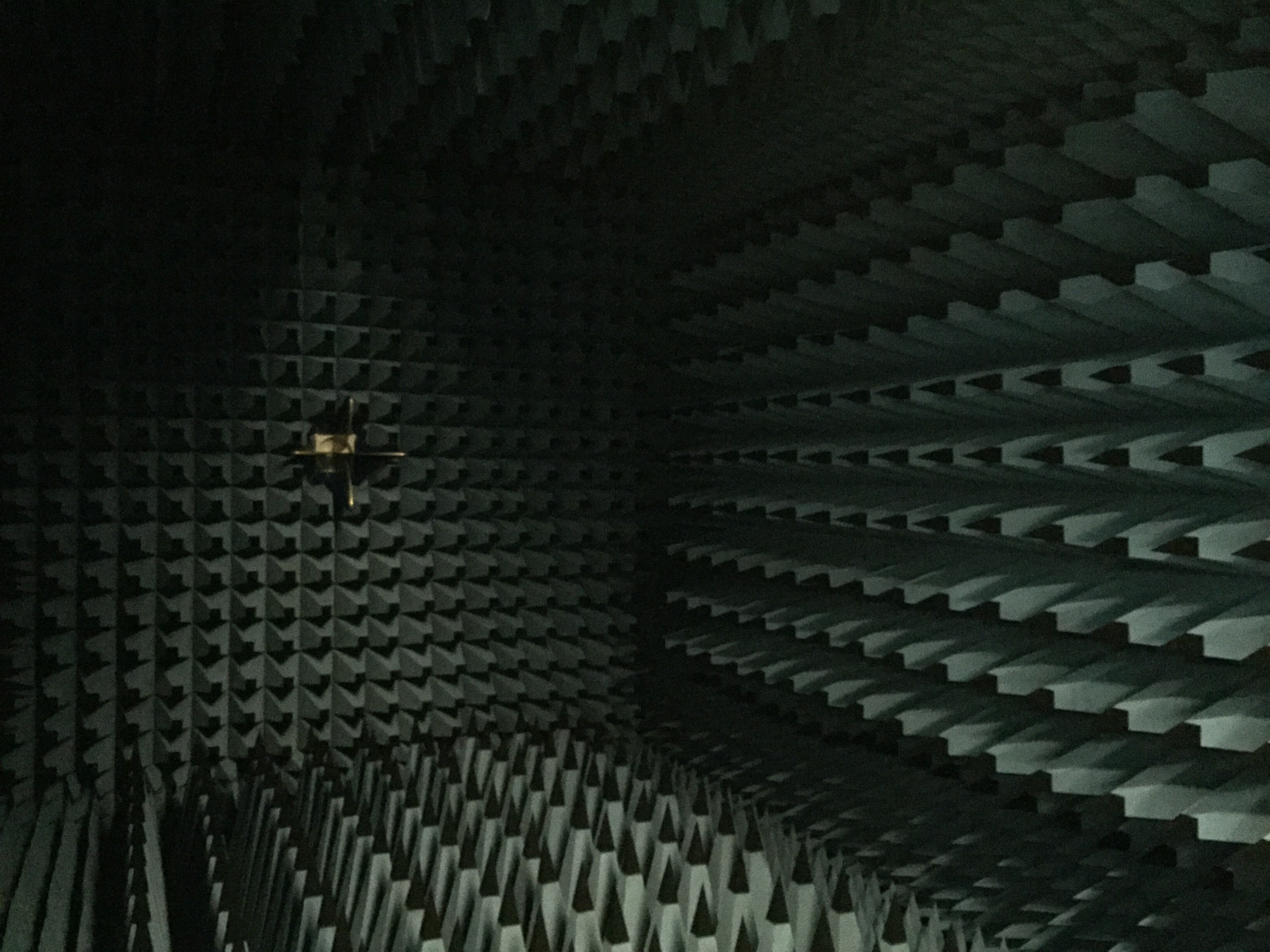
With the door closed, we couldn't hear anything from the outside. It was complete silence. Staying in the chamber for any amount of time above five minutes started to make us feel uncomfortable. We were told that if you stay in an anechoic chamber for long enough, you actually can hear the blood flowing through your ears, as well as your own heartbeat.
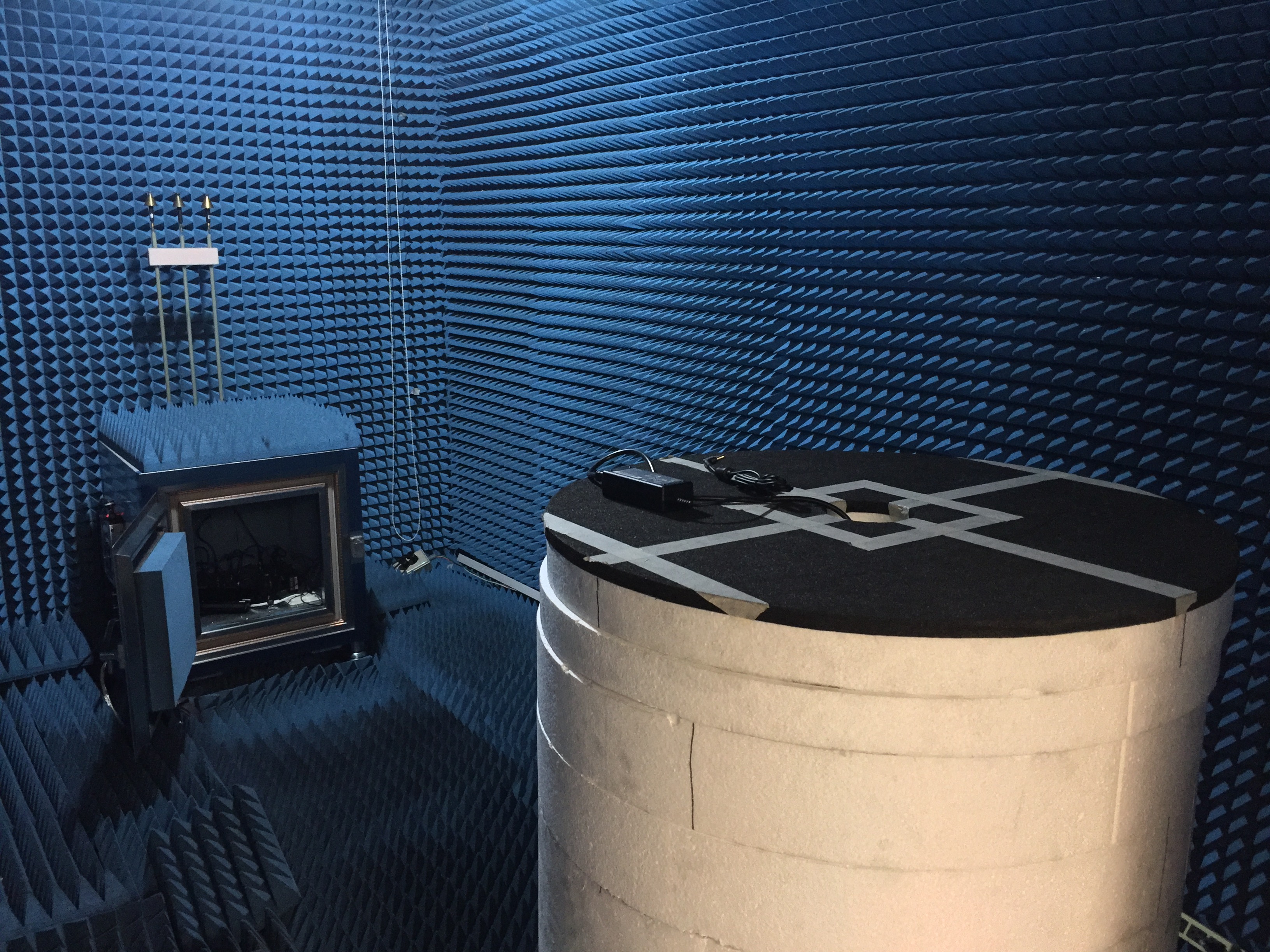
Above is another smaller anechoic chamber used to test Bluetooth- and Wi-Fi-related devices. For example, a router can be placed inside the box at the end, which is sealed from radio interference. The antennas are connected to the box itself, and the box has antennas on the outside. This ensures exact testing of antenna performance.
The pedestal closer to the camera is where receiving devices are placed.
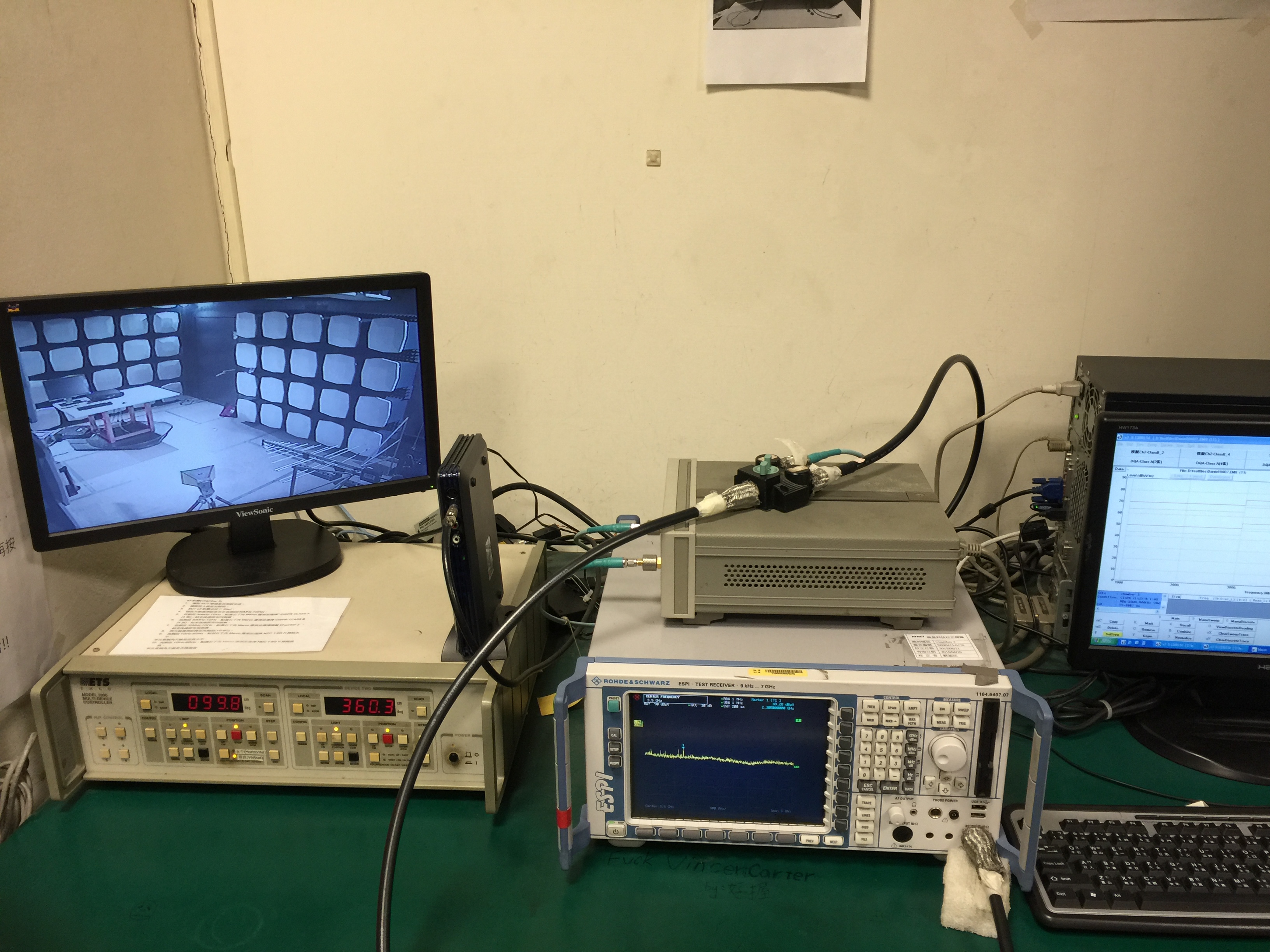
Testing equipment is connected and placed outside of the chamber, so as not to cause interference. A monitor shows the engineer what's going inside, and scopes provide signal readings.
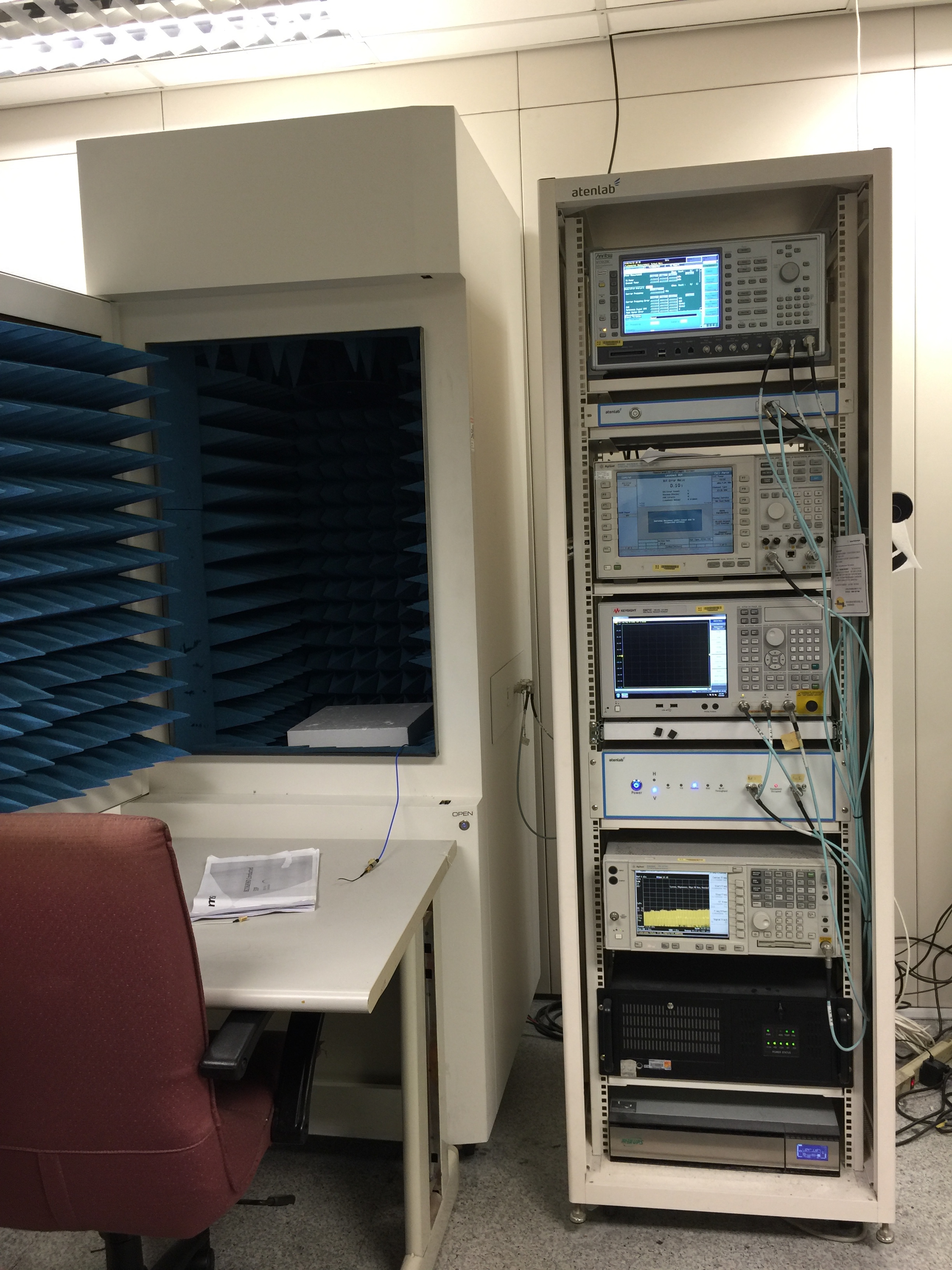
Anechoic chambers can come in all sizes. This one in particular is a mobile unit, but was still larger than a full server rack and heavy.
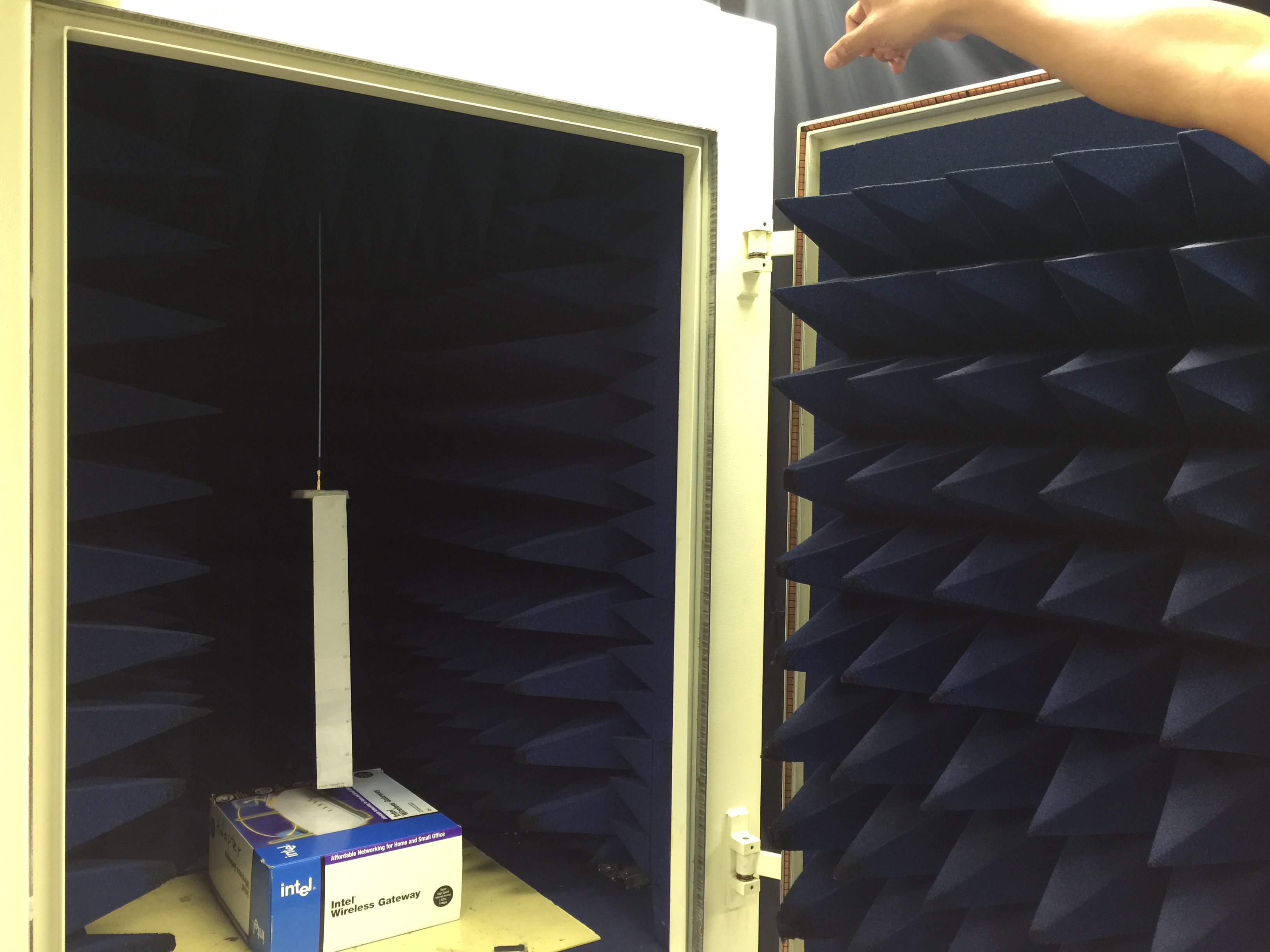
A wireless cellular dongle and its antenna is being tested in the above chamber. The wire from the antenna actually goes outside of the entire building.
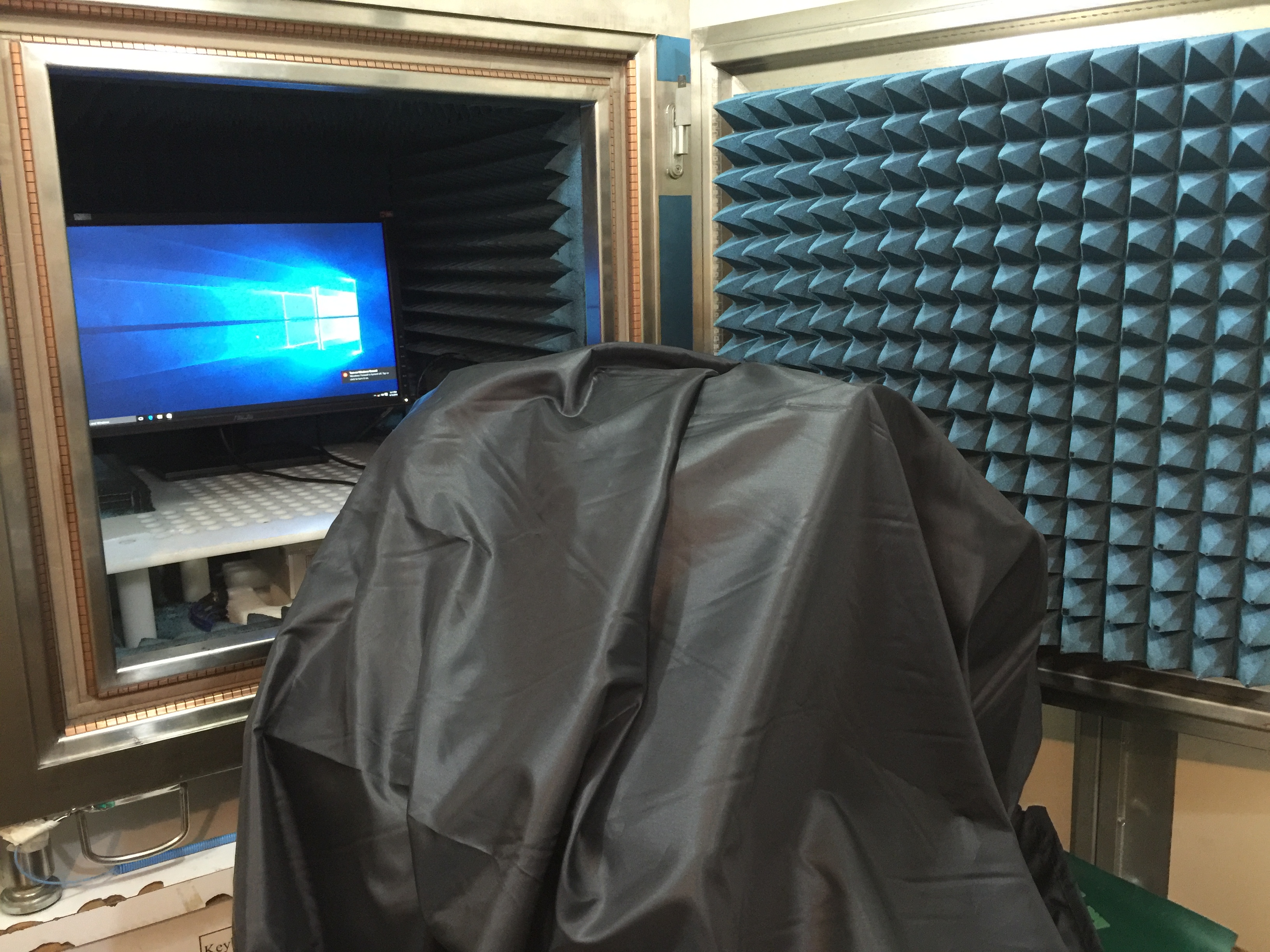
Sometimes entire PCs are tested. Here, an all-in-one computer is put into a chamber to test for interference and noise. All things get measured. Acoustics play a big role in fully built systems and there are tolerances that MSI must adhere to, depending on who the system will be sold to and where.
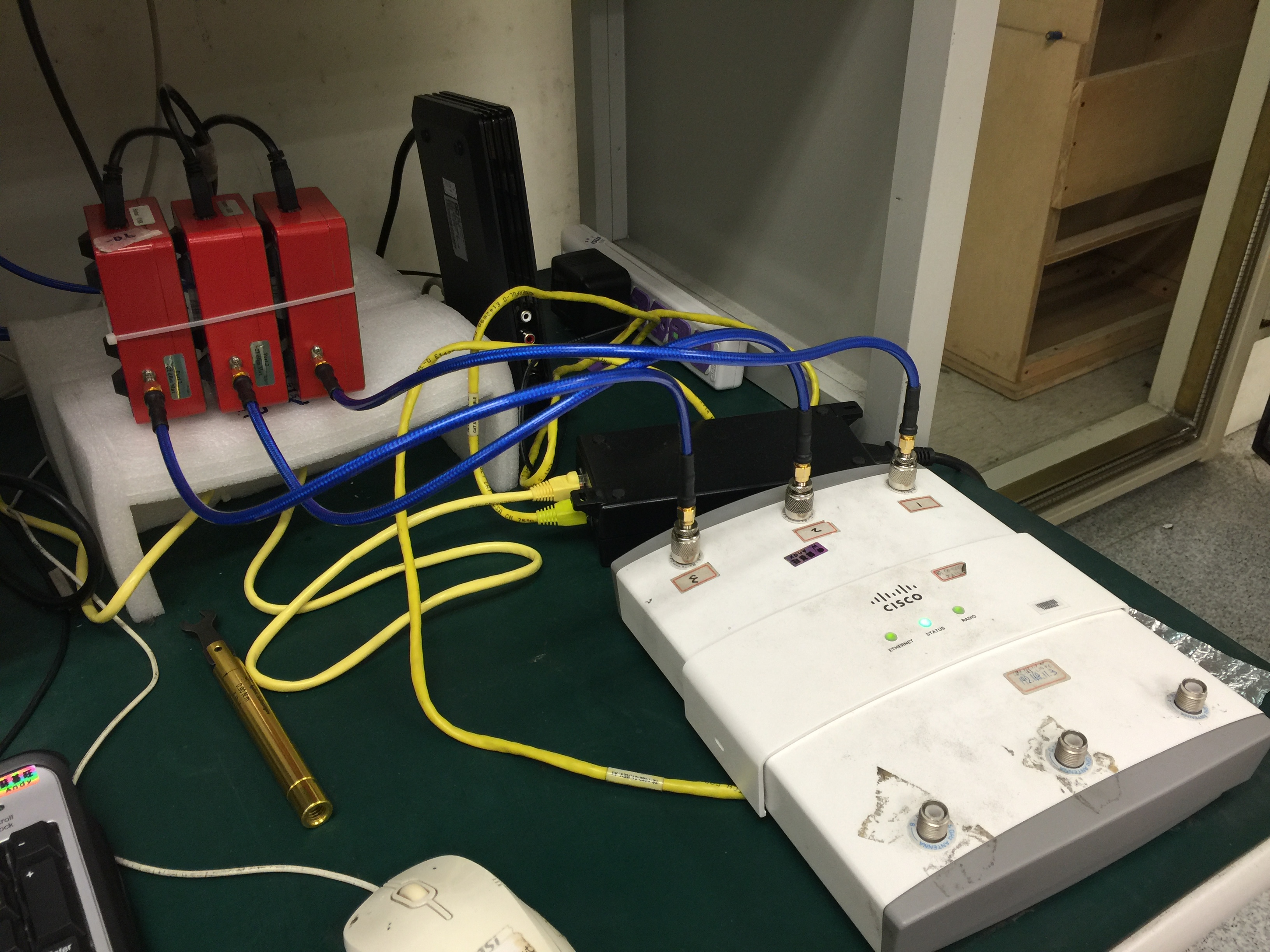
MSI's testing lab can test everything. From wireless performance, magnetic interference, grounding issues, to electrical shock resistance. Not seen in this photo is an electric gun used to zap products, inside and out. The gun can send out a zap that's anywhere between 10,000 and 30,000 volts.
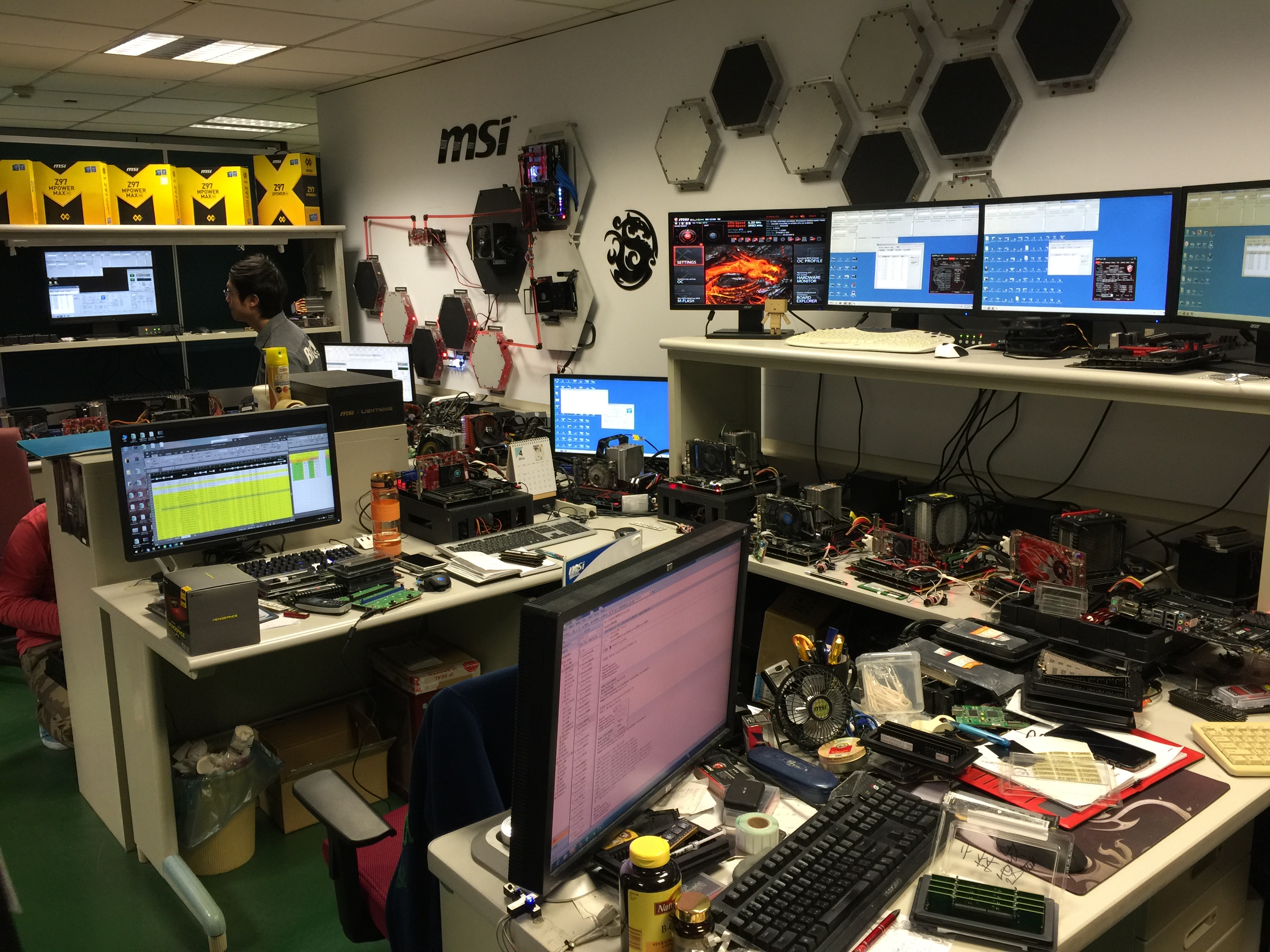
A testing lab stuffed with parts and half-built computers. Spot any components you recognize?
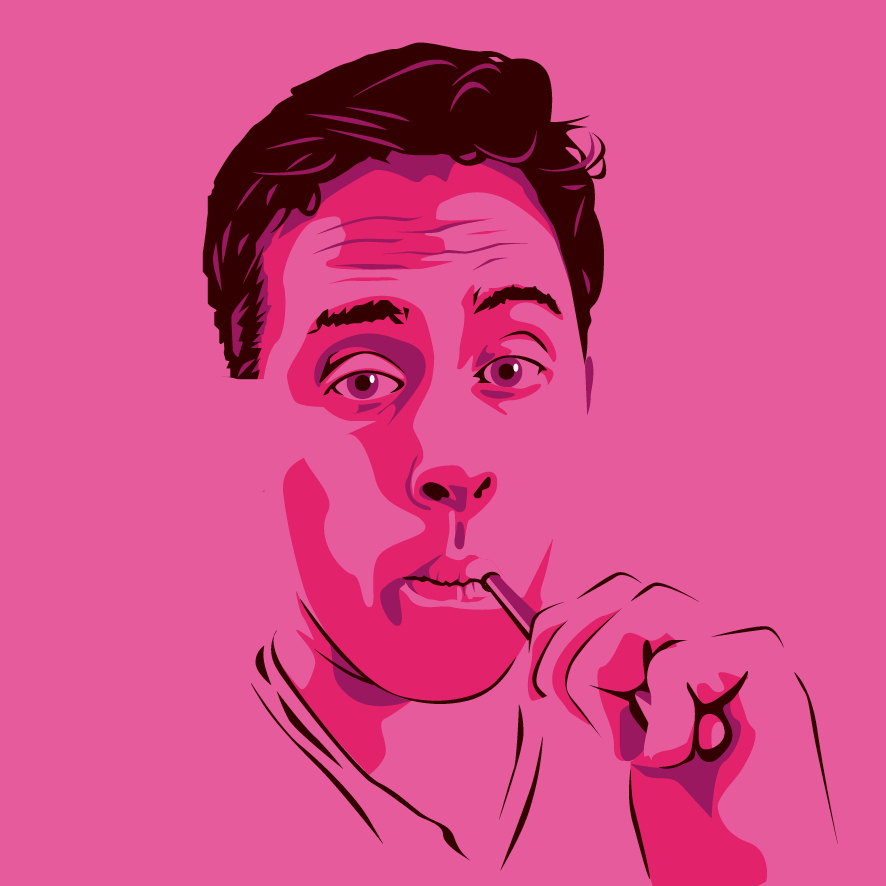
Wes has been covering games and hardware for more than 10 years, first at tech sites like The Wirecutter and Tested before joining the PC Gamer team in 2014. Wes plays a little bit of everything, but he'll always jump at the chance to cover emulation and Japanese games.
When he's not obsessively optimizing and re-optimizing a tangle of conveyor belts in Satisfactory (it's really becoming a problem), he's probably playing a 20-year-old Final Fantasy or some opaque ASCII roguelike. With a focus on writing and editing features, he seeks out personal stories and in-depth histories from the corners of PC gaming and its niche communities. 50% pizza by volume (deep dish, to be specific).